WITH DIAMOND-PLATED LAYER WITH A COMBINATION OF CVD AND HPHT DIAMONDS
In the process of dressing abrasive wheels with a traditional diamond dressing tool, the dispersed abrasive material actively washes out the bond in the places of laying synthetic single-crystal diamonds, and the latter fall out without using up their resource. At machine-building enterprises of Ukraine, for dressing modern abrasive wheels (when grinding the surfaces of rotation of complex-shaped products), imported dressing rollers with CVD diamonds are now being used. (CVD — Chemical Vapour Deposition — one of the new technologies for laboratory production of diamond products by chemical deposition from the vapor phase). The elongated shape of CVD diamonds and the greater depth of laying in the bond should stabilize their retention on the working surface of the tool, and therefore increase the resource of the dressing tool.
Ukrainian machine-building enterprises, especially for engine building, aggregate and hydraulic aggregate plants, and aviation enterprises, need a precision ruler, and it is available on the market, but it is an imported ruler from such companies as CORUS (Switzerland) (did not find such circles), “Shaundt” (did not find such circles) and Reishauer (Germany), TYROLIT (Austria). This tool is expensive and requires enterprises to have foreign currency. At the same time, to meet the needs of Ukrainian enterprises in it, as well as to enter the foreign market, it is in the National Academy of Sciences of Ukraine (in particular, in the V. M. Bakul Institute of Mechanical Engineering) that effective ruler tools are developed and produced. However, over time, there is a need for innovative improvement of this tool, which is the purpose of writing this article. Precision diamond tools for mechanical engineering require modern approaches to the formation of its surface layer in combination with the use of new diamond materials, which is one of the factors for improving its performance characteristics. Therefore, researchers are constantly paying attention to this issue. In this article, we will focus on the latest modern developments in the formation of the diamond-abrasive layer of the tool by electroplating, as well as on the use of a mixture of CVD and HPHT diamonds (synthetic diamonds obtained under high pressures and temperatures) and precision dressing of complex-profile abrasive wheels.
CVD diamonds are currently receiving some application in diamond tools, especially dressing. According to the Global CVD Diamond Sales Market Report, by 2026 the global CVD diamond market is expected to reach $568.9 million compared to $364.8 million in 2020, with an average annual growth rate of 7.7% from 2021 to 2026. As a result, Ukrainian machine-building enterprises are now starting to use imported dressing rollers with CVD diamonds for dressing modern abrasive wheels (when grinding the surfaces of rotation of complex-shaped products). During the dressing of abrasive wheels with a traditional diamond tool, the dispersed abrasive material actively washes out the bonds in the places where synthetic single-crystal diamonds are laid, and the latter fall out without using up their resource. The elongated shape of the CVD elements and the greater depth of laying in the bundle should stabilize their retention on the working surface of the tool, and therefore increase the resource of the dressing tool. On the other hand, the use of only CVD diamonds requires a large number of them on the periphery of the tool for kinematic reasons, otherwise the abrasive material of the wheel being dressed will wash away the bond already in the places where the CVD diamonds are laid, and they will fall out without using up their resource. Therefore, the analysis of modern developments in identifying the features of the formation of the galvanic working layer, especially with CVD diamonds, is relevant from the point of view of the development of modern domestic dressing tools. Thus, in the work [Kee Han Lee, Won Kyung Seong, Rodney S. Ruoff. CVD diamond growth: Replacing the hot metallic filament with a hot graphite plate. Carbon. 2022. Vol. 187. P. 396–403.] described how CVD diamond films (from nanocrystalline to polycrystalline) were synthesized by chemical vapor deposition, where a hot graphite plate was used for thermal activation of methane and hydrogen. The pressure was from 40 to 100 Torr, the methane concentration in hydrogen was from 0.5 to 2 vol.%, and the substrate temperature was from 1020 to 1140 °C. The maximum growth rate was 0.8 μm/h, and the quality was comparable to diamond films synthesized by chemical vapor deposition on a hot metal filament. The resulting diamond films do not contain metal impurities [Kee Han Lee, Won Kyung Seong, Rodney S. Ruoff. CVD diamond growth: Replacing the hot metallic filament with a hot graphite plate. Carbon. 2022. Vol. 187. P. 396–403.]. Work [The effect of UV and thermally induced oxidation on the surface and structural properties of CVD diamond layers with different grain sizes / Anna Dychalska, Marek Trzcinski, Kazimierz Fabisiak , Kazimierz Paprocki, Wojciech Koczorowski, Szymon Łoś, Mirosław Szybowicz. Diamond and Related Materials. 2022. Vol. 121. Art. 108739.] is a continuation of previously published studies on the influence of hydrogen treatment on the structural properties of polycrystalline CVD diamond layers with different grain sizes. Hydrogenated diamond layers were studied, which were oxidized in two stages: first by UV irradiation in air, and then by burning at 300 °C in air. It was found that microcrystalline and nanocrystalline diamond layers behave differently during oxidation (Fig. 1). In general, microcrystalline samples were more easily oxidized during UV treatment. The article [Sheng Wang, Qingliang Zhao, Bing Guo. Wear characteristics of electroplated diamond dressing wheels used for on-machine precision truing of arc-shaped diamond wheels. Diamond and Related Materials. 2022. Vol. 129. Art. 109372.] already directly concerns the technology of dressing. It studies in detail the wear characteristics of diamond dressing wheels with electroplated coating, which are used for precision dressing of arc-shaped diamond wheels (Fig. 2). The wear topography, the height of the protrusion of diamonds, as well as the wear mechanism of the metal matrix were studied. It was found that the dressing accuracy of diamond arc-shaped grinding wheels can be significantly improved by reducing the wear of diamond particles of the electroplated dressing tool. Graphitization appears in a dressing wheel with a large grain size of diamond particles, and the diamond wear rate will be accelerated. As an example, a D213 μm grain size cutting wheel successfully reduces the radial runout error of an arc-shaped diamond wheel with a hybrid bond from 35 μm to 1.9 μm. Given the above, let us proceed directly to the presentation of our research related to the use of CVD diamonds in a cutting tool. In this case, we were interested in polycrystalline CVD diamonds for strengthening problem areas of a diamond precision cutting tool. CVD diamond inserts 0.8×0.8×1.5 mm were analyzed using an electron microscope. The samples were examined by scanning electron microscopy at different magnifications on a ZEISS EVO 50XVP microscope equipped with an INCA450 energy-dispersive X-ray spectrum analyzer with an INCAPentaFETx3 detector and an HKL CHANNEL-5 system for diffraction of reflected electrons (manufactured by OXFORD). Two surfaces on one sample were analyzed: the original (Fig. 3a) and the polished (Fig. 3b). The elemental composition (% by mass) of the surfaces shown in Fig. 3: original — carbon (C) — 84.8, oxygen (O) — 12.1, aluminum — 3.1; polished — carbon (C) — 97.6, aluminum — 2.4.
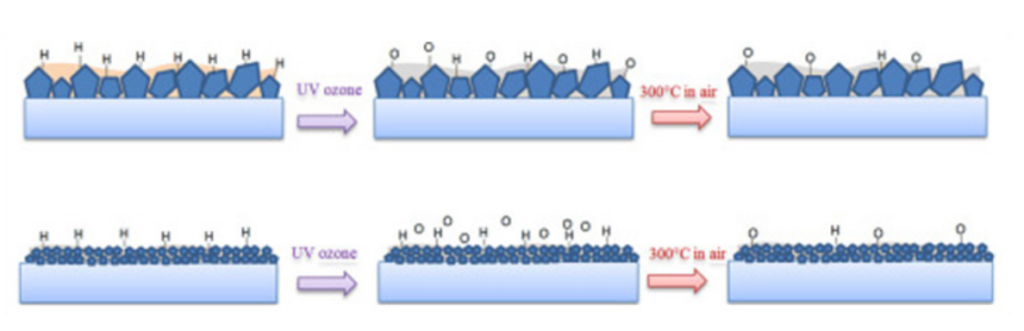
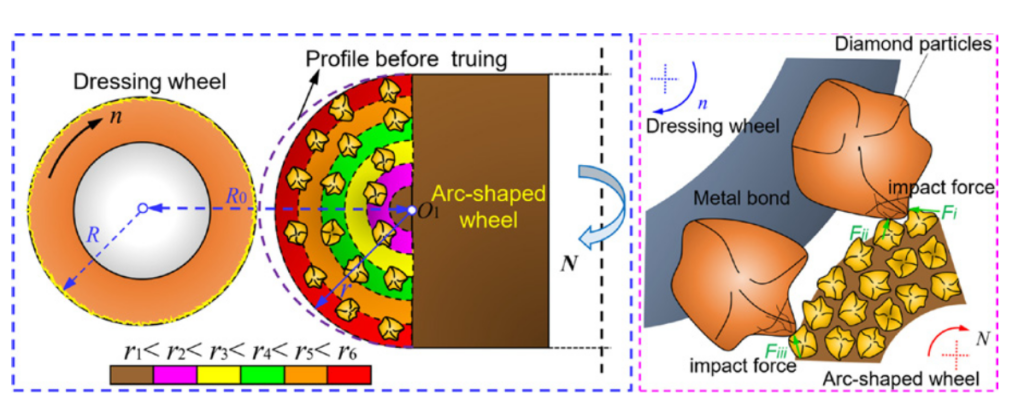
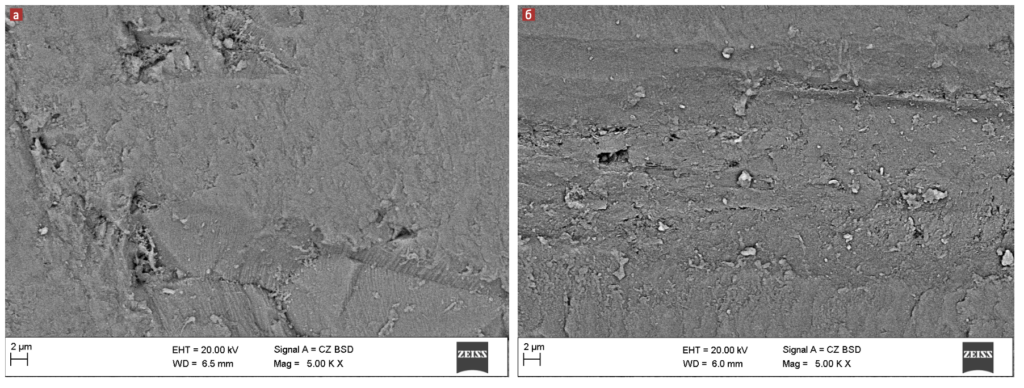
CVD diamonds (see Fig. 3) and from the scanning microscopy data, the following conclusions can be drawn:
- On the initial surface, its polycrystalline nature is observed, and you can even see certain grain boundaries, which the polycrystal itself consists of.
- On the initial surface of the CVD diamond, an increased amount of oxygen is observed, which is not present on the polished surface. That is, it is the initial surface of the CVD diamond, due to increased defects, that is also saturated with oxygen. In the case of the polished surface, we have a smooth surface (see Fig. 3b) and a complete absence of oxygen on it.
- Let us also pay attention to the fact that polycrystalline CVD diamonds contain a small (within 2–3% by mass) amount of aluminum.
Further work was devoted to the dimensional stability of straightening rollers manufactured by the electroplating method using CVD diamonds for the processes of abrasive shaping of surfaces of complex-shaped products. In the process of straightening abrasive wheels with a traditional diamond tool, the dispersed abrasive material actively washes away the bonds in the places of laying synthetic single-crystal diamonds, and the latter fall out without using up their resource. The elongated shape of the CVD inserts and the greater depth of laying in the bond should stabilize their retention on the working surface of the tool, especially in areas of the working profile of great curvature, and therefore increase the service life of the straightening tool. The use of CVD inserts in a straightening tool, the working layer of which is formed by the electroplating method, minimizes further fine-tuning of the CVD inserts to the corresponding working profile of the tool. The stability test of rollers with CVD diamonds was carried out on a special stand based on a 3B151 circular grinding machine with an autonomous drive of the dressing roller and by dressing abrasive wheels according to the grinding scheme with axial feed. To ensure such operating conditions for the diamond layer of the roller as during mortise dressing, the axial feed S, according to [Sheiko M. N., Pasichny O. O., Skok V. N., Bologov P. I. Quasi-mortise dressing of abrasive wheels as an express method of testing diamond shaped rollers. Communication 1. Registration of dressing forces. Superhard materials. 2009. No. 4. P. 65–75.], was equal to the length L of the section with protection by CVD inserts. The speed of the abrasive wheel (29 m/s) and the roller (14.6 m/s) corresponded to the dressing modes used in production conditions. Abrasive wheels Ø600×63×305 of the brand from 25А F60 J 7V (25M3) to 25А F60 N 7V (25CT1) were dressed at an axial feed S = 1.0 mm/rev (U = 18.3 mm/s) and a feed to a depth of t0 = 0.10 mm. The test was carried out according to a single-factor experiment plan, and the factors that varied were the number of CVD inserts on the working surface of the dressing tool and the characteristics of the dressed abrasive wheel – hardness, structure number and grain size. In order to intensify the experiments, laboratory rollers were designed with two rows of CVD inserts along the circumferences of the working surface, which lie on the edges of the straight profile (8 mm) of the tool and form two vertices with the radii of curvature RL and RR, respectively (Fig. 4). In this case, two values of the number of CVD inserts corresponded to one roller at once. The profile contained an understated (in our case by 1 mm) part that served as a base and did not contact the abrasive wheel during the main work, and therefore was not subject to wear. With respect to this base, linear wear (understatement of δ of the vertex) of the areas protected by CVD inserts was measured. Due to the discreteness of the working surface of the diamond roller, linear wear was measured indirectly, using a plate witness on a DIP-3 microscope with an accuracy of ± 2 μm. It was appropriate to record not the absolute current values of RL and RR, but those relative to the initial RL0 and RR0, respectively. The measurement of the absolute values of the underestimation δ and radii was carried out during the processing (scale adjustment, etc.) of photographs (in electronic form) of the corresponding profiles taken with a DIP-3 microscope.
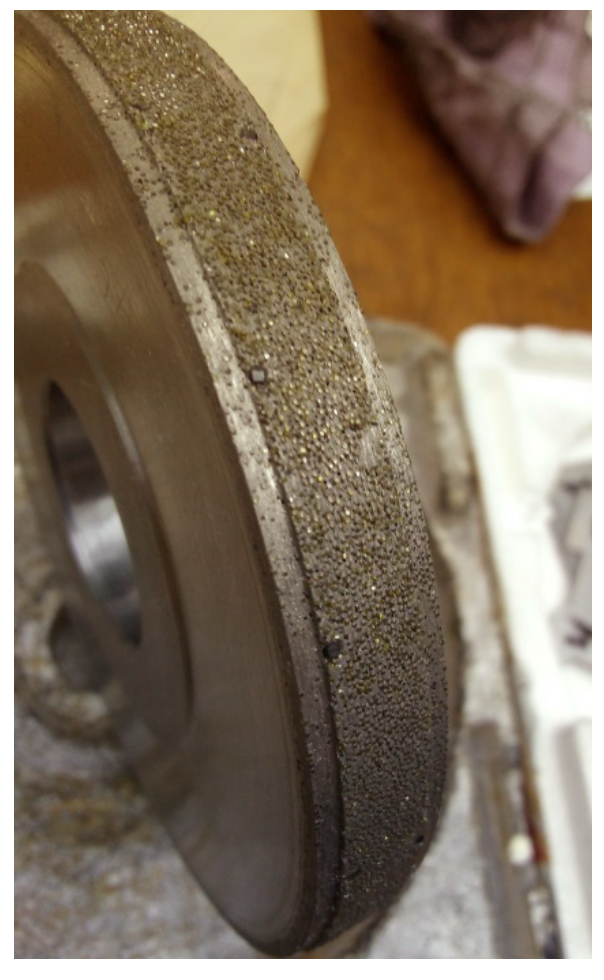
The relative values of the apex radii ?? were presented as a function of the volume of the dispersed abrasive material of the wheels, and for clarity the volume was measured in conventional units: one conventional unit is the volume of a cylinder Ø600 and 1 millimeter high. For this purpose, the primary materials were analyzed and processed, photographs of CVD inserts on the working surface of the dressing rollers at different stages of wear were taken, and summary tables of apex wear were constructed. The processing of experimental data showed that: firstly, the use of CVD inserts in the loaded areas of the dressing tool significantly increases the dimensional stability of the working profile, secondly, the wear of CVD diamonds, as well as HPHT crystals, under the conditions of dressing abrasive wheels on a ceramic bond has the character of abrasive wear. To conduct production tests of the CVD diamond dressing tool, samples of dressing rollers with a diameter of 150 mm for dressing gear grinding wheels were designed and manufactured. On both sides of the dressing roller, 90 CVD diamond crystals with a size of 0.8´0.8´1.5 mm (0.01 carat) were placed at four degrees from each other (Fig. 5).
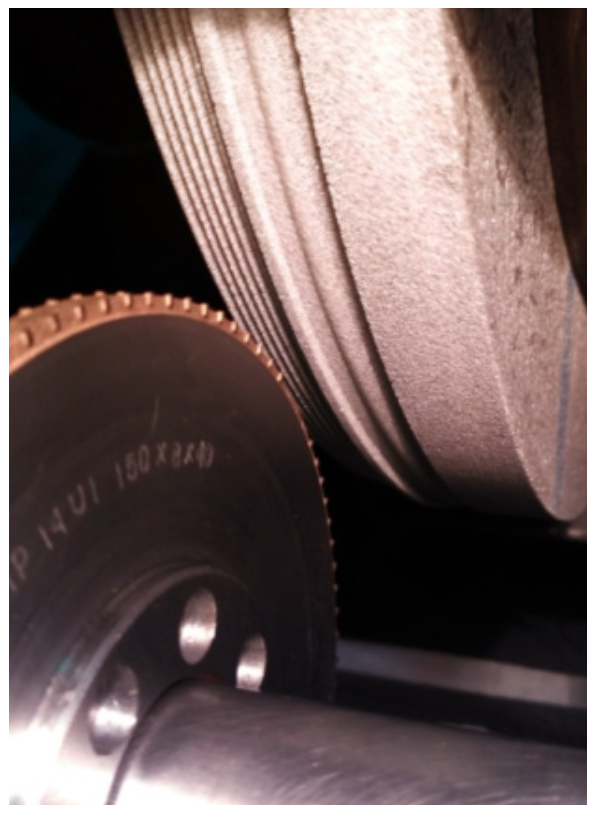
Fig. 5. CVD diamond roller when dressing a grinding wheel
As in the laboratory, the results of production tests showed that: firstly, the use of CVD inserts in the loaded areas of the dressing tool significantly increases the dimensional stability of the working profile, secondly, the wear of CVD diamonds, as well as HPHT crystals, in the conditions of dressing abrasive wheels on a ceramic bond has the character of abrasive wear. The use of such complex-profile areas in the tool, purposefully improved with a mixture of CVD and HPHT diamonds, allows you to increase the efficiency of the diamond dressing tool. The test results allow you to draw a positive conclusion about the prospects for import substitution of such a tool for the needs of machine-building enterprises in Ukraine. For questions about the manufacture of a special precision dressing tool and the implementation of effective diamond-abrasive dressing processes, as well as for more detailed information, you can contact the V. M. Bakul Institute of Metallurgical Engineering of the National Academy of Sciences of Ukraine, Department of Diamond-Abrasive and Physical-Technical Processing.
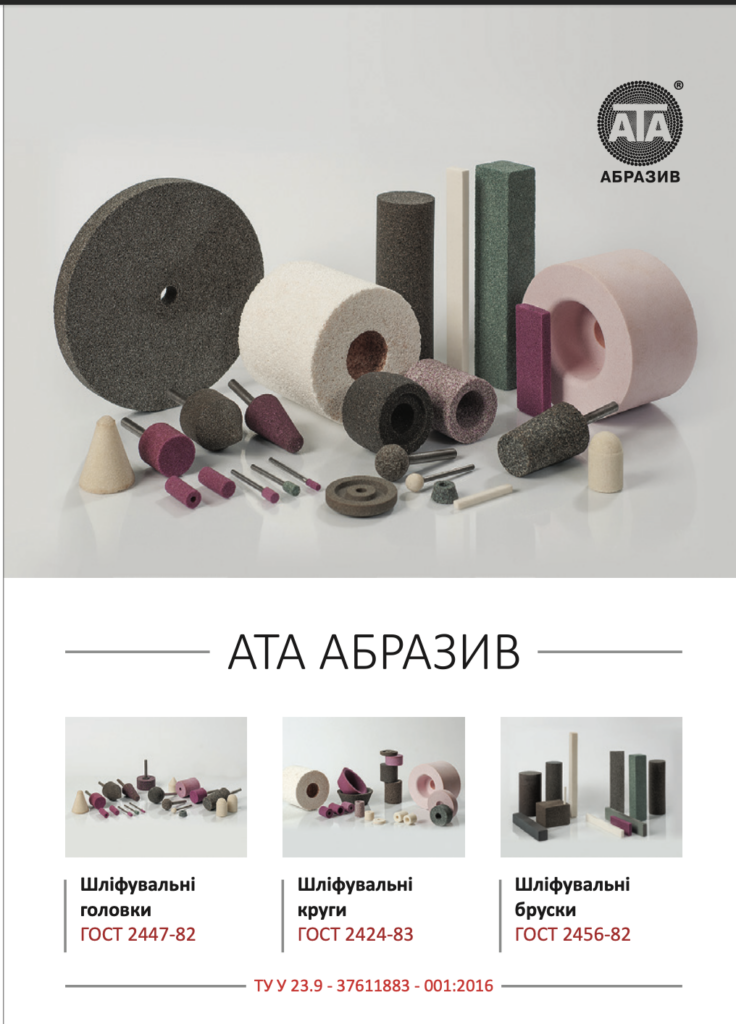
Properly selected abrasive tools are a necessary component of the production process at mechanical engineering enterprises. Tool manufacturing, bearing industry, machine tool manufacturing, automotive industry and oil and gas engineering, aircraft and shipbuilding, production of equipment for the light and food industries are just some of the branches of mechanical engineering that require high-quality abrasive tools.
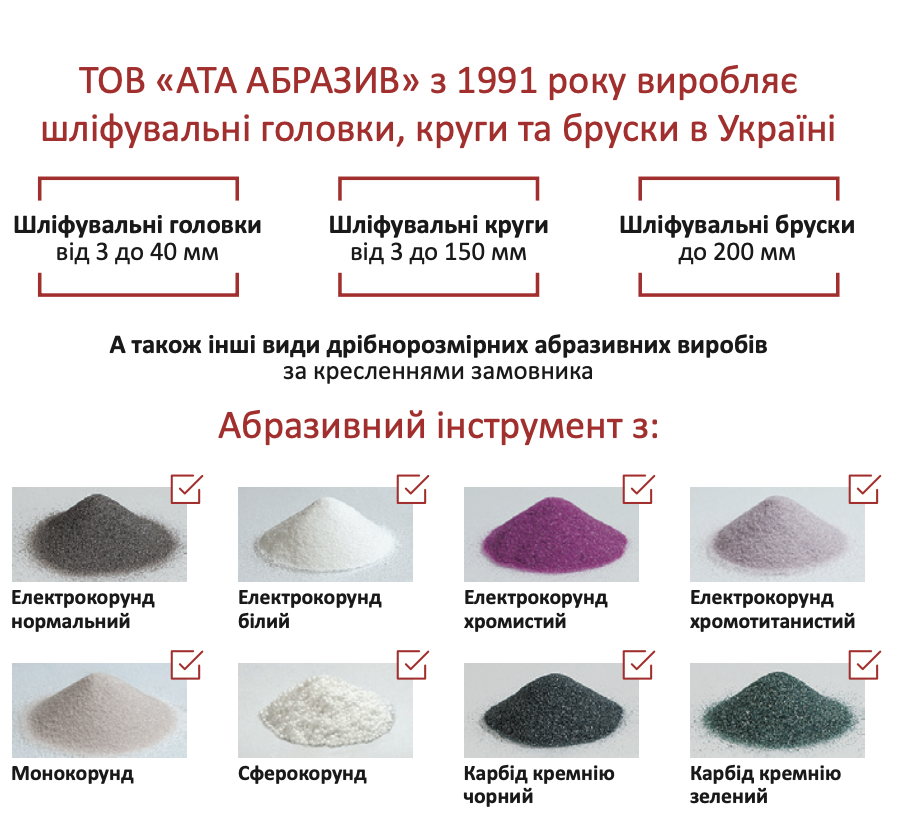
The use of abrasive materials from the best manufacturers, special ceramic bonds and fillers in the production technology, control at each stage of production ensure high resistance of the abrasive tool, high accuracy and excellent quality of the treated surface. It is possible to manufacture a tool with a grain size from F24 to F1000, hardness from M to T, as well as impregnation with sulfur and other substances.