1. INTRODUCTION
In mechanical engineering, diamond-abrasive processing accounts for a quarter of all operations, and in bearing, tool and optical-mechanical production more than 50%. It uses hard-to-process materials that can only be processed with efficient tools based on diamonds and cubic boron nitride. However, high-performance processing of such materials in the industry is carried out with diamond tools, in which the most used for processing are diamond grades of low strength AC4 and AC6, which have certain features – specific defect in the form of surface porosity and the presence of metal inclusions, left and non-metallic impurities [1], and therefore face the need for some improvement in their properties.
The process of diamond synthesis of AC4 and AC6 grades takes place at high crystal growth rates, which capture all the side phases present in the reaction chamber as they grow. A catalyst in the form of a solvent alloy is used to reduce the required high synthesis parameters. Detailed research and numerous works on the study of diamond synthesis process, mainly performed with the use of solvent alloys of the Ni–Mn–C system. In recent years, interest in the use of a cheaper solvent alloy, Fe–Si, has increased [2]. It should be noted that the issue of studying the inhomogeneity and defects of diamond grains is not given enough attention, because it is believed that there is no fundamental difference in the grains, there is only a certain difference in surface development, and they were considered continuous environment. Meanwhile, in the literature there are works on the study of the heterogeneity and defects of diamond grains, taking into account the metals they capture during synthesis.
In article [3] to explore the difficulty of diamond reacting with different kinds of metals and metal oxides, the activation energies of the reaction between diamond and metals, as well as between diamond and metal oxides, were obtained by first-principle calculation.
Magnetic mineral inclusions, as iron oxides or sulfides, occur quite rarely in natural diamonds [4]. The presence of iron impurities in synthetic diamonds made in the Fe–Si system is precisely the factor that changes the magnetic properties of such diamonds [1].
The presence of such inclusions in diamond allowed the authors of work [5] to obtain a new diamond with pores and increased self-sharpening or self-healing properties using the Fe/Fe2O3 thermochemical corrosion method. Electroless composite plating is a valuable way to prepare diamond magnetic abrasives [6].
We have paid more attention to thermochemical methods, and now we will pay more attention to thermal methods of impact on diamonds.
In work [7] describe a technique to improve diamond cutting tools used in nanometer- and micrometer-scale machining and formed via focused-ion-beam (FIB) micromachining. Heating at 500 °C was optimal to remove the non-diamond phase from the diamond tools [7].
In the article [8] another example of thermal influence is presented – plasma. In the article [9] was studied the effect of anodic oxidation of a natural type boron doped diamond single crystal (100) surface on both the tribocurrent and macroscopic friction force (~mN) when a nickel-coated steel needle slides on it with different normal forces.
Since we have considered the thermal effects of diamonds above, we are certainly faced with the issue of diamond oxidation. In [10] one of the options for solving this is shown. The polycrystalline diamond compact (PDC), which consists of a polycrystalline diamond layer on a tungsten carbide (WC)/cobalt (Co) substrate, is extensively utilized as drilling bits.
In [11] the situation when a diamond is in contact with a titanium alloy is considered. In [1], attention was drawn to the fact that, along with the temperature effect, a significant reason for the deterioration of the strength characteristics of synthetic diamonds is the violation of the crystal lattice due to defects. This is confirmed by the authors of the article [12], which shows that the observed local roughness at the boundary of diamond grains after mechanical friction, accompanied by frictional heat, is the main factor that causes surface roughness, which is affected by the thermal inhomogeneity of the expansion and contraction of the crystal, related with defects in differently oriented crystals formed as a result of a mechanical process.
The authors of [13] claim that when the limit values of the local temperature of 650–670°С are reached, chemical interactions of inclusions with diamond inside the grain take place. Features of such interaction can be used to achieve the effect of surface roughening on the interfacial thermal conductance, which is described in [14] for diamond/copper composites.
Thus, in diamonds in areas with a high concentration of vacancies, it is possible to combine them into micropores and even voids. Given that diamond is a diamagnetic, and the solvent alloys used in the synthesis have well-defined magnetic properties, it makes it possible to determine the content of surface impurities in diamond grain by magnetic method, and metal impurities in diamond crystals have a phase composition due to [1].
There are some data in the literature on the movement of impurities in diamonds [15, 16] during their heat treatment, but studies on a wide range of impurities, and therefore the values of the specific magnetic susceptibility of diamond grains have not been conducted, so in this article was given attention in this direction. It should be noted that we pay attention to the directed thermal influence, because this direction should lead to the movement of impurities in diamond in the direction of surface layers, promote their exit into pores and cracks, changes in the specific magnetic susceptibility of grains and, as a result, increase the strength of the grains, and hence the wear resistance of the grinding wheels.
2. DATA AND METHODOLOGY
In previous works [1, 17] we have shown that to adequately assess the properties of grinding powders of synthetic diamonds and the possibility of their targeted change, it is important to take into account the conditions of diamond synthesis, namely in which system they are synthesized. In [1], this is stated for grinding powders of low-strength diamonds (AC6 and AC20), which are used in grinding wheels for machining products. Earlier we [17] showed that heat treatment can effectively affect the properties of synthetic diamond grains using ferroalloys.
Note that diamond oxidizes when heated. The onset temperature of oxidation is estimated at 700–750 °С. And if we heat up to higher temperatures, we will meet with the phenomenon of graphitization, and hence with the gradual disappearance of diamond. Diamond graphitization is the forced rearrangement of a cubic diamond lattice into a hexagonal graphite lattice, which occurs at sufficiently high temperatures (1450–2000 °C), which corresponds to the conditions of breaking the bonds of atoms in the lattice, their redistribution and changes in distance between crystallographic planes. Graphitization occurs with an increase in volume by 1.5 times, so the formation of the embryo occurs by overcoming the elastic resistance of the medium. In the place of graphite formation, diamond is very tense. The perfect diamond crystal is graphitized mainly on the surface. If there are inclusions in the diamond, graphitization can also occur in the volume of the crystal [18].
In general, the graphitization of diamond is due to its catalytic phase transformation into graphite under the action of oxygen. Therefore, the temperature of the beginning of graphitization in the temperature range up to 1900 °C is determined by the presence of oxygen in the area of contact with the diamond. In [19] it was suggested that a similar effect on graphitization should be caused by any medium that interacts with diamond, for example, chemically active carbide-forming metals: Si, Ti, Cr, V, Mn, Fe , Co, Ni, and to a greater extent those metals in contact with which the interfacial energy of diamond is minimal. Graphitization of diamond during sintering is determined by the combined action of metal and oxygen. As the catalytic influence on the process of phase transformation of diamond into graphite during sintering increases, the metals are arranged as follows: Si, W, Ti, Ni, Cr, Mn. The activation energy of the phase transformation of diamond into graphite is maximum for Si (168 kJ/mol) and minimum for Mn (55 kJ/mol). The influence of metals that chemically interact with diamond on the process of its phase transformation into graphite is reduced mainly to a sharp increase in the rate of formation of surface carbon due to a decrease in the free surface energy of diamond at the boundary with metal, and reducing the activation energy of the process. Evaluation of the kinetics of carbide formation in the growth system of the carbide layer on the diamond surface under conditions corresponding to its stability shows that the interaction of diamond with metals in this case, its phase transformation into graphite does not occur [19].
In the present work [20], a study of the graphitization of microcrystals of synthetic diamond of cuboctahedral shape and the morphological and structural evolution occurring at 1600 °C during vacuum annealing is presented.
In connection with the above, we turn our attention to the work [21], somewhat theoretical, but devoted to the high-temperature effect on diamond and where a simple method is proposed of calculation of the upper limit of diamond melting temperature, based on the study of planar defects in it.
3. RESULTS AND DISCUSSION
Note also that when heating sufficiently strong (AC50–AC100) synthetic diamonds, an important factor that causes grain cracking is the internal temperature stresses arising from the thermoelastic mismatch of inclusions of the solid solution of the solvent metal (Ni+Mn) and diamond crystal lattice [22]. The inclusions of the solvent metal are stored in the diamond after synthesis and are concentrated mainly in the plane (111). Due to the fact that the modulus of elasticity of this eutectic and its coefficient of thermal expansion differ significantly (approximately 3.9 times) from the corresponding properties of diamond, when heated to sufficiently high temperatures, for example, 1400–1600 °C during sintering with a carbide matrix, the inclusion expands, creating an internal pressure in the cavity, which leads the grain to destruction, which is accompanied by the release of metal droplets on its surface [23]. Modeling and optimization of performance parameters of grinding is given in papers [24,25,26].
All this, above, just shows that diamond grains of sufficiently high strength (AC50–AC200) are more vulnerable to heat, in contrast to diamond grains of low (AC4–AC6) strength, and can be destroyed with sufficient high (for 1000 °C) heating. On low-strength diamonds with developed morphology, the release of solvent metals on the surface when heated not only does not lead to cracking of the grains, but also leads to the filling of defects in the surface cavities or porous space of the grains. Therefore, it is necessary to take into account such defects, namely to consider it not as a negative but a positive factor in finding ways to increase the wear resistance of grinding wheels due to possible changes in the impurity composition of the grain surface or filling the pore space of grains with necessary functional substances, directed, for example thermal, influence on the state of diamond grain surfaces.
There are some data in the literature on the movement of impurities in diamonds [15, 16, 27] during their heat treatment, but studies on such a wide range of impurities, and therefore the values of the specific magnetic susceptibility of diamond grains, have not been conducted, so in this article, attention was paid to this area. It should be noted that we pay attention to the directed thermal influence, because this direction should lead to the movement of impurities in diamond in the direction of the surface layers, promote their exit into pores and cracks, and, as a result, increase grain strength and hence the wear resistance of the grinding wheels.
At the first stage, to obtain an independent assessment of such a phenomenon as the occurrence of high impurities on the surface of diamonds, the samples of synthetic diamonds made in the Fe–Si–C and Ni–Mn–C growth systems of two fractions for each system (magnetic and nonmagnetic), which underwent heat treatment at 800 °С, were transferred to the Frantsevich Institute of Problems of Materials Science NAS of Ukraine. Using scanning electron microscopy (SEM), the content of diamonds with different magnetic susceptibility of impurities and inclusions and their elemental composition was evaluated. On the Cameca SX-50 device the element-by-element analysis of smooth and relief surfaces of cutting of diamond crystals after thermal influences was carried out. The elemental analysis of the surfaces of the faces of synthetic diamond crystals made in both systems, Ni–Mn–C and Fe–Si–C after their heat treatment, showed that on the surfaces of the faces of diamond there are bags and inclusions, which under the influence of high-temperature heating through cracks and pores came to the surface of the faces of crystals (Fig. 1).
It was found that these formations of impurities and inclusions on the surfaces of the faces of the crystals mainly consist of elements of the solvent alloy. For synthetic diamonds of the magnetic fraction made in the Ni–Mn–C system, the main composition is impurities of Mn, Ni and O, and for non-magnetic diamonds only traces of O and Ni are detected.
On the surfaces of the faces of diamonds of the Fe–Si–C system, the main composition of the formations are such elements as: Si, Al, Fe, O, Ca. As a result of the research, it was concluded that the surfaces of the faces of diamond crystals of the Fe–Si–C system have a more directed microrelief in comparison with diamond crystals of the Ni–Mn–C system. Thus, the above experiments showed that there are some changes in the content of the elements of the solvent alloy in the inclusions and impurities of the magnetic fraction in the presence of thermal effects on diamonds, and this may be seen by changes in their magnetic properties.
To do this, in the second stage of research for each of these systems were selected two samples of diamonds fraction distribution: magnetic (with the highest content of impurities) and low-magnetic (with the lowest content of impurities), which were subjected to heat treatment at 500 to 1000 °C with a holding time of 20 min. At the same time evaluated the weight loss of the corresponding sample powder when heated to the same temperatures. It was found that both studied systems are characterized by the presence of a temperature range where the specific magnetic susceptibility of diamond powder increases, but the nature of the dependences “temperature – specific magnetic susceptibility” is different.
The magnetic susceptibility of Fe–Si–C diamond powders increases, and reaches a maximum at a heat treatment temperature of 800 ˚С. This effect is the same for both magnetic (Fig. 2, a) and non-magnetic powders (Fig. 2, b), but it is in the presence of a large number of inclusions, as expected from our assumption, the effect is more tangible.
Note that with increasing temperature, the weight loss of diamond powder increases, and on less magnetic powders such a loss is more noticeable and at 1000 °C in both cases it increases significantly, and thus significantly reduces the specific magnetic favorability, actually returning to the original state.
The magnetic susceptibility of synthetic diamond powders made the Ni–Mn–C system also changes with changes in the heat treatment temperature, but the nature of the changes is completely different than that of Fe–Si–C diamonds. There is also the effect of increasing the specific magnetic susceptibility and also at the heat treatment temperature of 800 °C reaches a maximum.
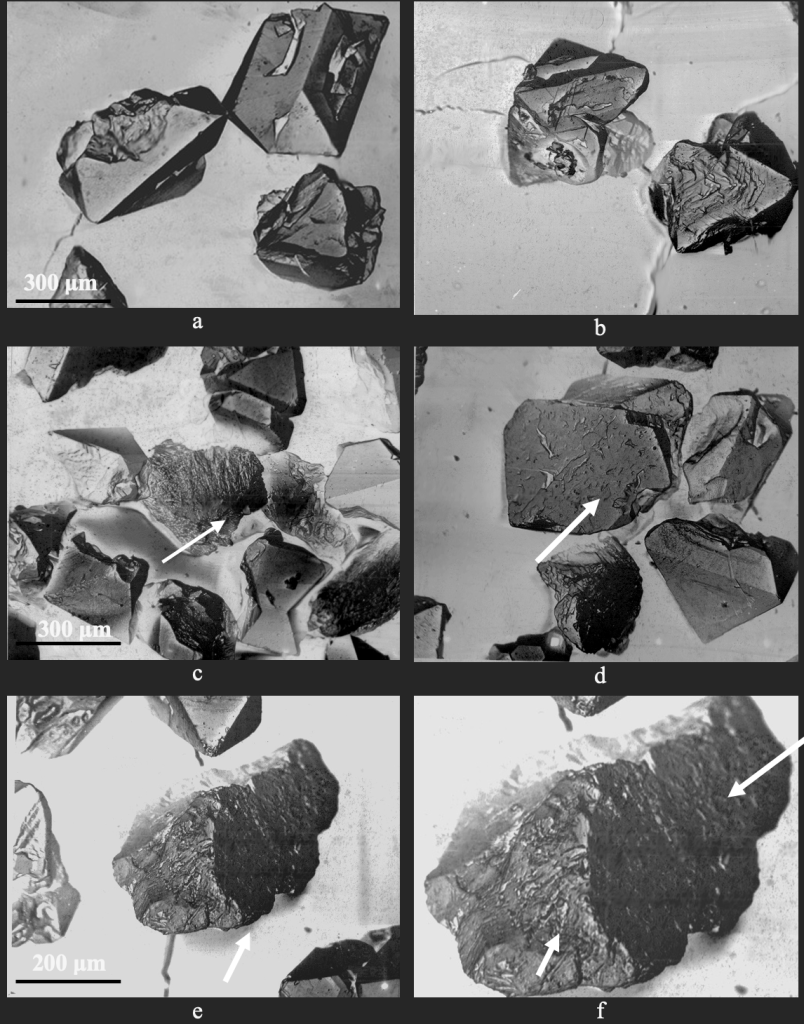
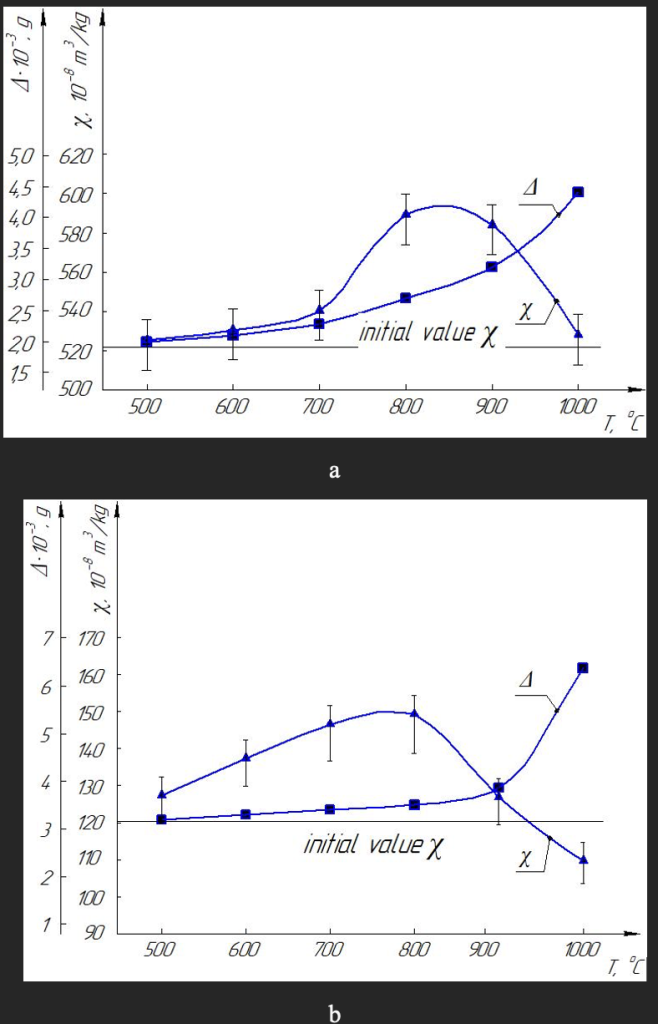
But this happens only in magnetic powders (Fig. 3a), and for non-magnetic powders it is actually absent (Fig. 3b). In our opinion, this is due to the relatively low content of inclusions in such diamonds, the amount of which is insufficient for the positive effect of increasing the effect of magnetic susceptibility. Among other things, we note that with increasing temperature, as in diamonds of the Fe–Si–C system, the weight loss of diamond powder also increases, but in diamonds of the Ni–Mn–C system such a loss is much greater, and this is likely affects the fact that when the temperature exceeds 800 °C in both cases (see Fig. 3), the value of specific susceptibility is significantly reduced from the values for the original, not heat-treated powder.
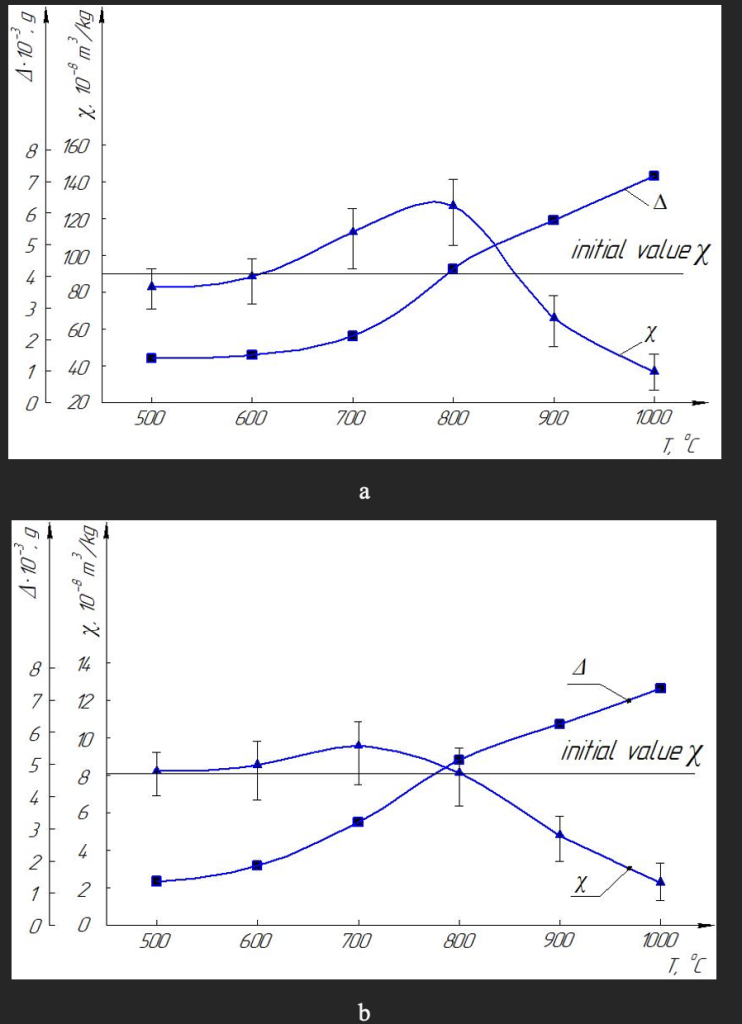
The above regularities indicate that for magnetic grains it is possible to expect an increase in the values of strength (destructive load) of diamond grains during heat treatment. The grain strength of diamond grinding powders of AC6 160/125 grain size was determined according to the method of DSTU 3292-95 after heat treatment for a number of magnetic and nonmagnetic fractions of the Fe–Si–C system, as well as Ni–Mn–C.
The dynamics of change in strength for the most magnetic diamond powders of both synthesis systems depending on the value of the heat treatment temperature is shown in Fig. 4. It was found that the strength of diamonds of the Fe–Si–C system with increasing heat treatment temperature to 700 ºC remains the same as the original, increases at 800 and 900 ºC.
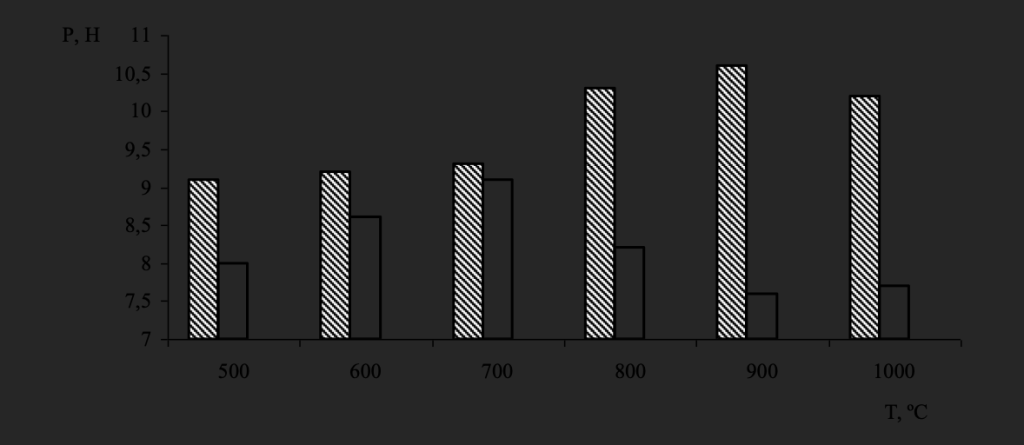
And then it has a descending character, starting with 900 ºC. At the same time, the strength of the separated magnetic fraction of the grinding powder of diamonds of the Ni–Mn–C system has an increase at 700 ºС and then decreases.
The general nature of changes in grain strength is reminiscent of the nature of changes in the value of magnetic susceptibility during heat treatment. Therefore, we analyzed the whole array of data obtained on the values of grain strength and the corresponding values of the specific magnetic susceptibility for a number of magnetic and nonmagnetic grains of the fractions of the Fe–Si–C system (Fig. 5, a) and Ni–Mn–C (Fig. 5, b). Data analysis of fig. 5 shows that both for synthetic diamond grains the Ni–Mn–C system and for synthetic diamonds the Fe–Si–C system, the effect of increasing the strength of grains under the action of thermal action is triggered only if when there is a sufficient number of inclusions in diamonds, and hence their increased magnetic susceptibility.
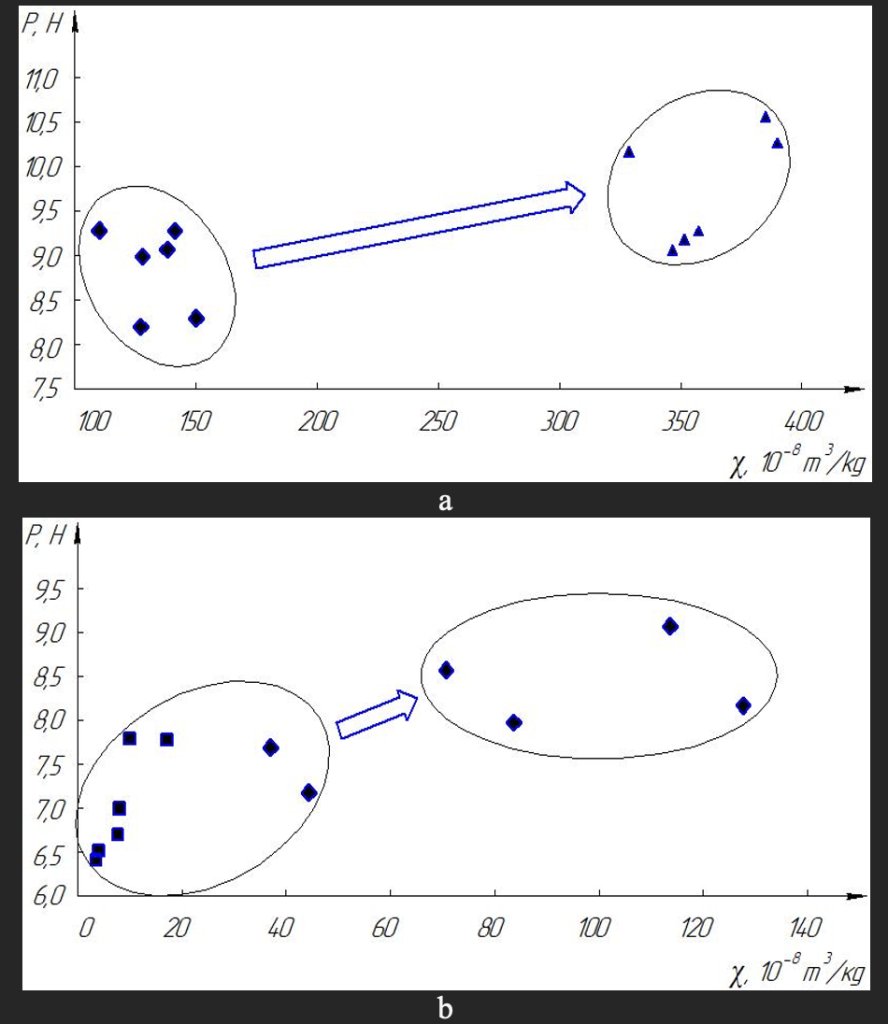
Fig. 5. Cluster correlation between specific magnetic susceptibility and destructive load (strength) of diamonds when heating magnetic and non-magnetic fractions of Fe–Si–C (a) and Ni–Mn–C (b).
That is why magnetic synthetic diamonds are the Fe–Si–C system and give a noticeable effect in increasing the strength of grains (see Fig. 4) during heat treatment, and thus in the possibility of increasing the wear resistance of grinding wheels. This is primarily due to the fact that such magnetic diamonds, having a significant (up to 7 % wt.) number of inclusions have a significant mass base for the movement of impurities and inclusions during heat treatment to ensure the effect of “healing” diamond surface defects.
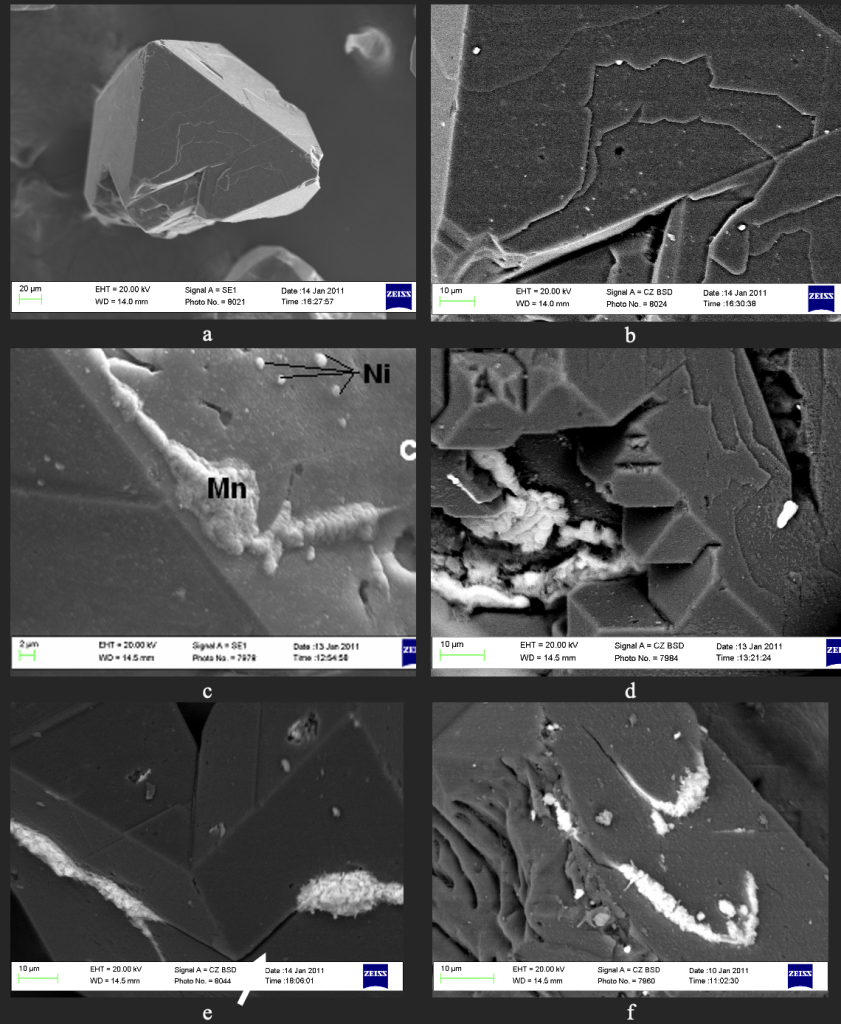
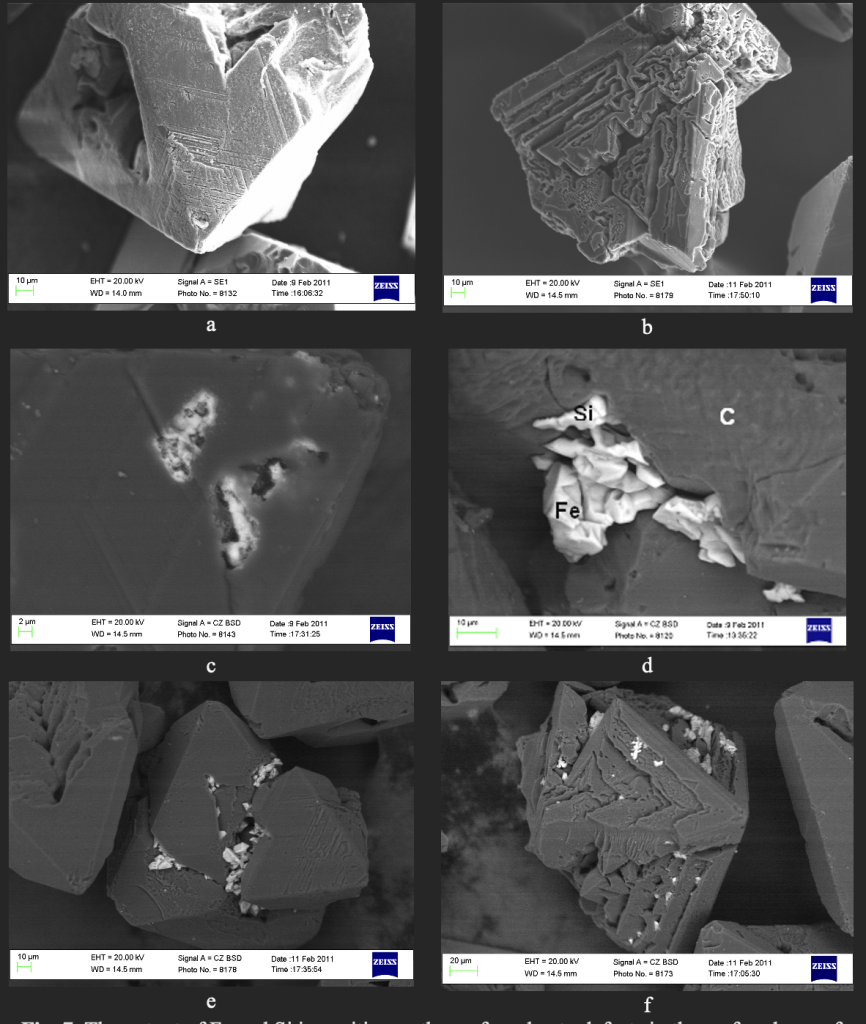
To confirm this assumption, the elemental composition and surface changes of diamond grains were examined using a Zeiss EVO 50XVP electron microscope. For synthetic magnetic grains (c=90•10-8 m3/kg) the Ni–Mn–C system, the presence of pores and cracks is characteristic (Fig. 6a, b). It is established that after heat treatment at 700 °С (Fig. 6c, d) and 1000 °С (Fig. 6e, f), the output of inclusions and filling of cracks and pores is observed. Similarly, the magnetic fraction of synthetic diamond made in the Fe–Si–C growth system (c=521•10-8 m3/kg) is characterized by the presence of pores and cracks (Fig. 7a, b). It was found that after heat treatment at 800 °C (Fig. 7c, d) and 1000 °C (Fig. 7e, f), there is an output of inclusions and filling cracks and pores.
Analysis of the elemental composition of inclusions and impurities in pores, cracks and on the surface of diamond grains was performed for synthetic diamonds made in the Fe–Si–C growth system (c=521•10-8 m3/kg) after heat treatment at 800 °С (Fig. 8, Table 1). Data analysis Table 1 indicates the predominant presence of Fe and Si in these impurities and inclusions.
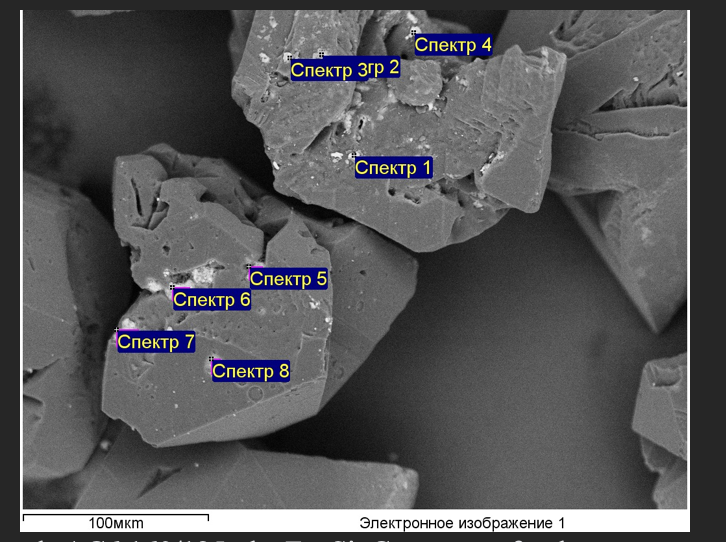
Table 1. Elemental composition of inclusions in the pores and on the surface of the grains (see Fig. 8).
Spectrum | Content of elements, % wt. | ||||||
C | O | Si | Fe | Cr | Mn | Ni | |
1 | 42,28 | 34,96 | 2,66 | 18,60 | 0,71 | 0,50 | 0,23 |
2 | 61,01 | 18,87 | 10,19 | 1,54 | 5,23 | 1,35 | 1,42 |
3 | 77,09 | 16,32 | 2,44 | 3,37 | 0,33 | 0,28 | 0,16 |
4 | 33,22 | 37,70 | 4,15 | 22,83 | 0,63 | 0,85 | 0,52 |
5 | 44,67 | 23,14 | 20,32 | 0,63 | 1,29 | 9,39 | 0,38 |
6 | 31,78 | 16,68 | 25,45 | 3,22 | 1,52 | 10,99 | 0,34 |
7 | 25,33 | 45,47 | 23,16 | 1,14 | 0,23 | 4,53 | 0,13 |
8 | 26,39 | 29,18 | 32,72 | 0,06 | 0,79 | 10,05 | 0,76 |
Thus, the above indicates that the thermal effect on the studied diamonds of low strength depending on the number, type of impurities and inclusions allows to change the surface elemental composition of diamonds, the magnitude of the specific magnetic susceptibility of grinding powders, diamond strength to increase its value, and therefore expect to increase the wear resistance of the grinding tool.
To do this, we previously, diamonds brand AC6 grain size 160/125 of both of the above growth systems, were distributed according to the value of their initial specific magnetic susceptibility: c=90•10-8 m3/kg for synthetic diamonds made in the system Ni–Mn–С, and c=521•10-8 m3/kg for synthetic diamonds made in the Fe–Si–С growth system. Diamonds were subjected to heat treatment for 20 minutes at a temperature of 700 °C for the first and 800 °C for the second (see Fig. 4). Then grinding wheels with identical characteristics were made, containing diamonds with different content of inclusions and investigated under the same conditions.
Separated in the magnetic field fractions of powder granularity 160/125 were tested in the treatment of hard alloy VK8. For the study, four grinding wheels of the form 12A2-45° AC6 160/125 50 M1-10 were made using diamonds with different specific magnetic susceptibility. Two wheels had original diamonds for both growth systems, and the other two diamonds were heat treated as described above. Processing of the hard alloy ВK8 was carried out on the machine 3B642 end of the wheel. Modes of processing: speed of rotation of a wheel – 15 m/s, longitudinal giving – 0,6 m/min, cross giving – 0,05 mm/pdv.h. Lubricating and cooling liquid – soda solution. The wear resistance of grinding wheels was assessed by the relative costs of diamonds qp (Table 2).
Table 2. Relative costs of diamonds in wheels when grinding a hard alloy ВK8 (Q = 300 mm3/min)
Growth system | Condition of diamond grains | χ, х108 m3/kg | Нр, Н | Costs, qр, mg/g |
Ni–Mn–С | Initial | 90 | 7,8 | 3,7 |
Heat treated | 150 | 9,1 | 2,3 | |
Fe–Si–С | Initial | 521 | 8,8 | 1,9 |
Heat treated | 589 | 10,3 | 0,9 |
Data analysis showed that depending on the system of synthesis, impurities and inclusions in diamonds and, accordingly, the value of their specific magnetic susceptibility of heat treatment of grains can increase up to 2 times the wear resistance of diamond grinding tools when grinding hard alloy.
4. CONCLUSION
An important feature of diamond powders, which affects the wear resistance of diamond tools, is the growth system in which they are synthesized. Knowing in which growth system a diamond is synthesized, it is possible to control its physico-mechanical and physico-chemical characteristics.
It is shown that diamonds contain inclusions of elements of the composition of the alloy-solvent and they can be divided into magnetic and non-magnetic (minimum values of the magnetic value) fractions. This allows you to control the properties of diamonds, for example, heat treatment.
The studied diamonds of low strength, having structural defects and surface defects can be strong sides of the crystal at a certain temperature of exposure to them.
The effect of heat treatment on diamond grains with high (magnetic) and low value (non-magnetic) inclusions of elements in the alloy-solvent composition of various Ni–Mn–C and Fe–Si–C growth systems showed that it allows controlling the strength of such grains, which is positive for their application in the tool.
REFERENCES
- Lavrinenko, V.I., Ilnitskaya, G.D., Petasyuk, G.A., at al. A study of the potential of improving performance of AS20 diamond powders through altering their dimensional and physico-chemical characteristics. Journal of Superhard Materials, 40 (4), 274–281. (2018).
- Borimsky, A.I., Delevi, V.G., Nagorny, P.A. Kinetics of diamond formation and growth in the Fe-Si-C system [in Russian]. Superhard Materials, 3, 9-14. (1999).
- Deng, A., Lu, J., Li, D.-X., Wang Y.-H. Exploring the activation energy of diamond reacting with metals and metal oxides by first-principle calculation. Diamond and Related Materials, 118, 108522. (2021).
- Piazzi, M., Morana, M., Coisson, M., Marone, F., Campione, M., Bindi, L., Jones, A.P., Ferrara, E., Alvaro, M. Multi-analytical characterization of Fe-rich magnetic inclusions in diamonds.Diamond and Related Materials, 98, 107489. (2019).
- Li, J.-W., Fang, W.-J., Wan, L., Liu, X.-P., Hu, W.-D., Cao, D., Han, K., Li, Y.-Y., Yan, Y.-G.: Research on the bonding properties of vitrified bonds with porous diamonds and the grinding performance of porous diamond abrasive tools. Diamond and Related Materials. 123, 108841. (2022).
- Yang, B., Lu, W.-Z., Feng, W., Yang, X., Zuo, D.-W. Adsorption and deposition of micro diamond particles in preparing diamond magnetic abrasives by electroless composite plating. Diamond and Related Materials, 73. 137-142. (2017).
- Kawasegi, N., Ozaki, K., Morita, N., Nishimura, K., Sasaoka, H. Single-crystal diamond tools formed using a focused ion beam: Tool life enhancement via heat treatment. Diamond and Related Materials, 49, 14-18. (2014).
- Geis, M.W., Hollis, M.A., Turner, G.W., Daulton, J., Varghese, J.O., Klyukin, K., Wang, J., Yildiz, B., Zhang, B. Controlling the carrier density of surface conductive diamond. Diamond and Related Materials, 122, 108775. (2022).
- Escobar, J.V., Chakravarty, A., Putterman, S.J.. Effect of anodic oxidation of single crystal boron doped diamond on tribocurrent and macroscopic friction force with metals. Diamond and Related Materials, 36, 8-15. (2013).
- Sha, X.-H., Yue, W., Zhang, H.-C., Qin, W.-B., She, D.-S., Wang, C.-B. Thermal stability of polycrystalline diamond compact sintered with boron-coated diamond particles. Diamond and Related Materials, 104, 107753. (2020).
- Wan, Q.-H., Zou, L., Liu, S.-Q., Wang, T.-T., Chen, S.-T., Huang, Y. Investigation on abrasive wear mechanism of single diamond grain in flexible scribing titanium alloy. Diamond and Related Materials, 120, 108631. (2021).
- Liang, Y.-F. Zheng, Y.-T., Wei, J.-J., Jia, X., Zhu, X.-H., An, K., Liu, J.-L., Chen, L.-X., Li, C.-M.. Effect of grain boundary on polycrystalline diamond polishing by high-speed dynamic friction. Diamond and Related Materials, 117, 108461. (2021).
- Chmir, M.Ya., Mogilnikov, V.A., Troitskiy, N.A., Gerasimenko, V.K. Interaction of synthetic diamonds with machined materials at diamond and diamond-electrochemical grinding [in Russian]. Electrochemical and Electrophysical Methods of Materials Processing: Collection of Scientific Works, Tula, 1991. pp. 52-59.
- Wu, X.-Z., Li, L.-Y., Zhang, W., Song, M.-X., Yang, W.-L., Peng, K. Effect of surface roughening on the interfacial thermal conductance of diamond/copper composites. Diamond and Related Materials, 98, 107467. (2019).
- Belyankina, A.V. Influence of high-temperature annealing on structure of single crystal of synthetic diamond [in Russian]. Synthetic Diamonds, 3, 22-24. (1971).
- Bacon, A. Investigation of changes occurring in diamond powders during reheating [in Russian]. Superhard Materials, 6, 20-23. (1983).
- Shulzhenko, A.A., Prikhna, T.O., Ilnytska, H.D., Lavrinenko, V.I., Borymskii, O.I., Sokolov, A.N., Tkach, V.N., Smokvyna, V.V., Zaitseva, I.N., Tymoshenko, V.V. Comparison of the dimensional, physical, mechanical and operational characteristics of as6 and AS20 synthetic diamond powders synthesized in the Ni‒Mn‒C and Fe‒Si‒C systems. Journal of Superhard Materials, 43 (1), 1–14. (2021).
- Tsypin, N.V. Wear resistance of composite diamond-containing materials for drilling tools [in Russian]. Nauk. dumka, Kyiv, 1983. – 192 pp.
- Nozhkina, A.V. Influence of metals on phase transformation of diamond into graphite [in Russian]. Superhard Materials, 3, 11-15. (1988).
- Bokhonov, B.B., Dudina, D.V., Sharafutdinov, M.R. Graphitization of synthetic diamond crystals: A morphological study. Diamond and Related Materials, 118, 108563. (2021).
- Kondrin, M.V., Lebed, Y.B., Brazhkin, V.V. Intrinsic planar defects in diamond and the upper limit on its melting temperature. Diamond and Related Materials, 110, 108114. (2020).
- Lavrinenko, V.I., Ilnitskaya, G.D., Sheiko, M.N., Dobroskok, V.L., Ostroverkh, Ye.V., Solod, V.Yu. Improving the performance characteristics of synthetic diamond for high-precision diamond dressing tool. Science and Innovation, 17 (6), 72–82. (2021).
- Novikov, N.V., Maistrenko, A.L., Kulakovsky, V.N. Fracture resistance of superhard composite materials [in Russian]. Nauk. dumka, Kyiv, 1993. – 220 pp.
- Tonkonogyi, V., Dašić, P., Rybak, O., Lysenko, T. Application of the modified genetic algorithm for optimization of plasma coatings grinding process. Lecture Notes in Networks and Systems (LNNS), 76, 199–211. (2020). doi: 10.1007/978-3-030-18072-0_23.
- Tonkonogyi, V., Yakimov, A., Bovnegra, L. Increase of performance of grinding by plate circles. Lecture Notes in Networks and Systems (LNNS), 42, 121–127. (2019). doi: 10.1007/978-3-319-90893-9_14.
- Usov, A., Tonkonogyi, V., Dašić, P., Rybak, O. Modelling of temperature field and stress-strain state of the workpiece with plasma coatings during surface grinding. Machines, 7 (1), Article no. 20. (2019). doi: 10.3390/machines7010020.
- Belyankina, A.V., Multakh, L.M., Simkin, E.S., Sozin, Y.I., Tsypin, N.V. Investigation of changes occurring in diamonds during heating [in Russian]. Synthetic Diamonds, 1, 20-22. (1972).