Methods for growing single crystals of diamond of types Ib, IIa and IIb in the region of thermodynamic stability have been developed, which provide controlled introduction of nitrogen and boron impurities into the crystal structure and make it possible to vary the electrophysical properties in such a way that the grown diamonds are suitable for the manufacture of active and passive components of electronic devices. Compared to silicon, such diamonds are able to withstand 5·103 times higher current density and 30 times higher operating voltage, and are resistant to the effects of extremely high temperatures and concentrated ionizing radiation.
Since the electrophysical properties of any material are structurally dependent, scientists determined and optimized the composition of solvents necessary for growing perfect, defect-free single crystals, developed algorithms and growth process cycles, and ultimately obtained experimental, structurally perfect, undoped and boron-doped (1018 – 1020 cm-3), single-crystal samples up to 20 mm in size, which are characterized by a minimal content of uncontrolled impurities and structural defects and have a dislocation density of no more than 1×103 cm-2. It was also determined that the main reason for the discrepancy in the current-voltage characteristics of diamond single crystals is their sectoral heterogeneity, respectively, the conditions for the formation of single-sector growth zones 100, 111 and 113 were found, from which plane-parallel plates with dimensions of about 1×1 cm2 and a thickness of 0.3 – 0.8 mm can be produced, that is, the so-called vertical p+/- Schottky diodes. In order to prevent a decrease in the height of the potential barrier and an increase in leakage currents caused by crystal surface defects and the formation of ohmic contacts, single-sector diamond plates cut from large single crystals are subjected to mechanical polishing, treatment in oxygen-hydrogen plasma to an average roughness of the working surface of several nanometers.
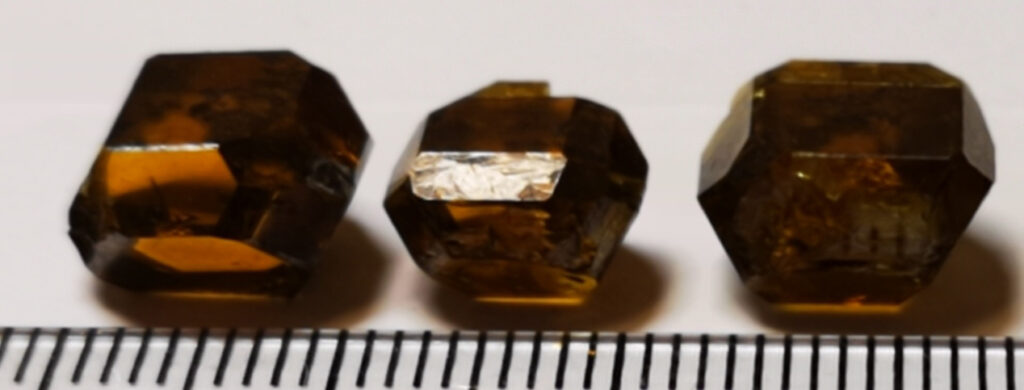
The modern high-pressure equipment available at the institute allows the process of growing such large, and most importantly, structurally perfect single crystals of diamond, using growth cells with a volume of 200 cm3 and more and increased growth productivity per cycle. Thus, there are prospects for the widespread use of synthetic diamonds, which were previously associated mainly with tool production, in solid-state power electronics, for example, powerful microwave devices, high-frequency radars, radiation and chemical detectors, etc.
The authors of the development – Ivakhnenko S.O. and Lysakovsky V.V.
By joint efforts of the employees of the Highway Institute and the Institute of Problems of Materials Science named after I.M. Frantsevich of the NAS of Ukraine, promising application materials for medical purposes for the treatment of patients with wound infection and severe purulent-septic diseases of a bacterial nature have been developed based on activated carbon nanostructured fibrous material with immobilized silver nanoparticles (AVVNM/Ag). AVVNM, which is obtained by chemical-thermal treatment of hydrated cellulose fibers, depending on the treatment temperature, consists of endless, more than 500 cross-sections long, macromolecules of cross-layered, cone-layered and rolled carbon nanofibers of cylindrical shape, oriented along the main direction, and the voids between the fibers are partially filled with graphite nanopackets and, mainly, granular SiO2 particles. Such a multiphase oriented fractal structure of the fiber forms a regular and homogeneous system of mesopores, which provides a large multifunctional surface and a significantly higher sorption capacity of the material compared to activated carbon. Concentrated suspensions of nanosilver are obtained using the “wet-dry” method of dispersing a metal cathode by a localized glow discharge in a vacuum.
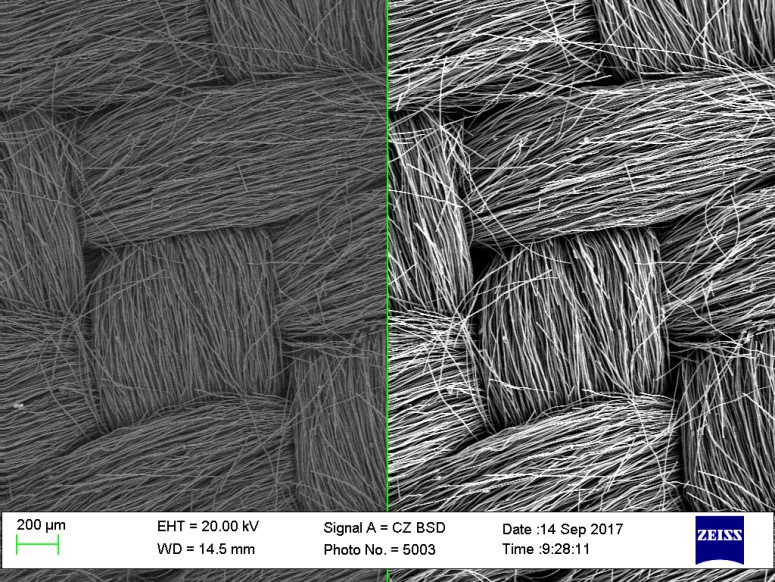
After that, the carbon fabric is immersed in a silver suspension for 15 min., applying ultrasound, which intensifies the sorption processes, as a result of which silver nanoparticles are adsorbed by the porous structure of the carbon matrix and form agglomerates on the surface of the fibers. And, since the retention of nanoparticles on the inner surfaces of the mesopores is carried out due to capillary forces, which are tens of times higher than all other forces responsible for adhesion, silver can be stored inside the AVVNM for a surprisingly long time without deterioration of its bactericidal properties.
Authors of the development – Sergeyev V.P., Loginova O.B., Kisterskaya L.D., Boshitskaya N.V., Klipov V.D.
A technology and tools have been developed for the final mechanical processing of parts that are restored by surfacing in repair facilities. Usually, bringing such parts to the dimensions specified in the drawing is difficult, since the instability of the chemical composition and properties of the surfacing material, the presence of macro- and micro-roughnesses on the surfacing surface cause instability of the process of interaction with the tool, negatively affect its performance indicators, processing accuracy characteristics and surface quality. Therefore, for manual mechanical processing of parts surfacing with high-hardness alloys, grinding wheels and grinding heads made of ruby-corundum and special heads made of synthetic diamond powders on a galvanic bond, which are characterized by increased wear resistance and resistance to salting, have been proposed. It was also determined that the optimal grinding speeds of welded parts with an abrasive tool should be 20-28×103 rpm, and with a diamond tool, respectively, 10-17.5×103 rpm.
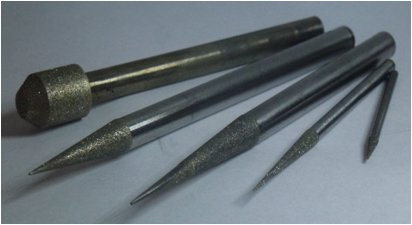
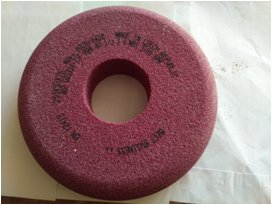
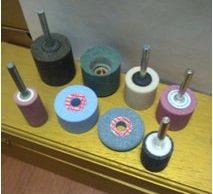
Grinding wheels made of chromium electrocorundum, for example, demonstrated high processing efficiency in flat grinding of wear-resistant surfaces of special dies, welded with the CastoDur N 9060 alloy, to a specified roughness of the welded surface of the products Ra 1.32. Testing of the developed tools and technology in the conditions of the Lutsk repair plant “Motor” showed that they allow to obtain the specified surface quality and manufacturing accuracy of aircraft engine parts, and also provide an increase in the processing productivity of parts welded with heat-resistant alloys ZhS6 and ZhS32 by 1.5–1.7 times compared to the tools currently used at the enterprise.
The authors of the development are Klymenko S.A., Ryabchenko S.V., Kopeykina M.Yu.
THE MOST SIGNIFICANT SCIENTIFIC RESULTS OF THE INSTITUTE IN 2020.
THE MOST SIGNIFICANT SCIENTIFIC RESULTS OF THE INSTITUTE IN 2021.
THE MOST SIGNIFICANT SCIENTIFIC RESULTS OF THE INSTITUTE IN 2022.