1. ВСТУП
У машинобудуванні алмазно-абразивна обробка займає чверть усіх операцій, а в підшипниковому, інструментальному та оптико-механічному виробництві — понад 50 %. Він використовує важкооброблювані матеріали, які можна обробити лише ефективними інструментами на основі алмазів і кубічного нітриду бору. Проте високопродуктивну обробку таких матеріалів у промисловості здійснюють алмазним інструментом, в якому для обробки найбільше використовують алмазні марки низької міцності АС4 і АС6, які мають певні особливості – специфічний дефект у вигляді поверхневої пористості та наявності металевих включень, лівих і неметалічних домішок [1], а тому потребують деякого поліпшення своїх властивостей.
Процес синтезу алмазів марок АС4 і АС6 відбувається при високих швидкостях росту кристалів, які захоплюють всі побічні фази, присутні в реакційній камері, під час росту. Для зниження необхідних високих параметрів синтезу використовується каталізатор у вигляді сплаву розчинника. Детальні дослідження та численні роботи з вивчення процесу синтезу алмазу, переважно з використанням сольвентних сплавів системи Ni–Mn–C. Останніми роками зріс інтерес до використання більш дешевого розчинного сплаву Fe–Si [2]. Слід зазначити, що питанням вивчення неоднорідності та дефектності алмазних зерен приділяється недостатньо уваги, оскільки вважається, що принципової різниці в зернах немає, є лише певна різниця в розвитку поверхні, і вони вважалися суцільним середовищем. Тим часом у літературі є роботи з вивчення неоднорідності та дефектності алмазних зерен з урахуванням металів, які вони захоплюють при синтезі.
У статті [3] для дослідження труднощів реакції алмазу з різними видами металів і оксидів металів енергія активації реакції між алмазом і металами, а також між алмазом і оксидами металів була отримана шляхом розрахунку з першого принципу.
Магнітні мінеральні включення, такі як оксиди або сульфіди заліза, зустрічаються в природних алмазах досить рідко [4]. Наявність домішок заліза в синтетичних алмазах, виготовлених у системі Fe–Si, є саме тим фактором, який змінює магнітні властивості таких алмазів [1].
Наявність таких включень в алмазі дозволила авторам роботи [5] методом термохімічної корозії Fe/Fe2O3 отримати новий алмаз з порами та підвищеними властивостями самозагострення або самовідновлення. Цінним способом одержання алмазних магнітних абразивів є безелектрологічне композитне покриття [6].
Більше уваги ми приділяли термохімічним методам, а тепер приділимо більше уваги термічним методам впливу на алмази.
У роботі [7] описано методику вдосконалення алмазних ріжучих інструментів, які використовуються в нано- та мікрометрових масштабах обробки та сформовані за допомогою мікрообробки сфокусованим іонним променем (FIB). Нагрівання при 500 °C було оптимальним для видалення неалмазної фази з алмазних інструментів [7].
У статті [8] наведено інший приклад теплового впливу – плазмовий. У статті [9] досліджено вплив анодного окислення поверхні монокристалу (100) алмазу, легованого бором, як на трибострум, так і на макроскопічну силу тертя (~мН), коли нікельована сталева голка ковзає по ній з різними нормальними силами.
Оскільки вище ми розглянули термічні ефекти алмазів, ми, безсумнівно, зіткнулися з проблемою окислення алмазів. В [10] наведено один із варіантів розв’язання цієї проблеми. Полікристалічний алмазний компакт (PDC), який складається з шару полікристалічного алмазу на підкладці з карбіду вольфраму (WC)/кобальту (Co), широко використовується як свердла.
В [11] розглядається ситуація, коли алмаз контактує з титановим сплавом. В роботі [1] звернуто увагу на те, що поряд з температурним впливом суттєвою причиною погіршення міцнісних характеристик синтетичних алмазів є порушення кристалічної решітки внаслідок дефектів. Це підтверджують автори статті [12], яка показує, що спостережувана локальна шорсткість на межі алмазних зерен після механічного тертя, що супроводжується теплом тертя, є основним фактором, який викликає шорсткість поверхні, на яку впливає термічна неоднорідність розширення та звуження кристала, пов’язана з дефектами в різноорієнтованих кристалах, утворених у результаті механічного процесу.
Автори [13] стверджують, що при досягненні граничних значень локальної температури 650–670°С відбуваються хімічні взаємодії включень з алмазом усередині зерна. Особливості такої взаємодії можуть бути використані для досягнення ефекту шорсткості поверхні на міжфазну теплопровідність, яка описана в [14] для композитів алмаз/мідь.
Так, в алмазах в областях з високою концентрацією вакансій можливе їх об’єднання в мікропори і навіть порожнечі. Враховуючи те, що алмаз є діамагнетиком, а використовувані при синтезі сплави-розчинники мають чітко виражені магнітні властивості, це дає змогу визначати вміст поверхневих домішок у зерні алмазу магнітним методом, а металеві домішки в кристалах алмазу мають фазовий склад, обумовлений [1].
У літературі є деякі дані щодо руху домішок в алмазах [15, 16] під час їх термічної обробки, але дослідження широкого спектру домішок, а отже і значень питомої магнітної сприйнятливості алмазних зерен не проводились, тому в даній статті було приділено увагу цьому напрямку. Слід зазначити, що звертаємо увагу на спрямований термічний вплив, оскільки цей напрямок має призводити до переміщення домішок в алмазі в напрямку поверхневих шарів, сприяти їх виходу в пори і тріщини, зміні питомої магнітної сприйнятливості зерен і, як наслідок, збільшенню міцності зерен, а отже, і зносостійкості шліфувальних кругів.
2. ДАНІ ТА МЕТОДОЛОГІЯ
У попередніх роботах [1, 17] ми показали, що для адекватної оцінки властивостей шліфувальних порошків синтетичних алмазів та можливості їх цілеспрямованої зміни важливо враховувати умови синтезу алмазів, а саме в якій системі вони синтезовані. В [1] це зазначено для шліфувальних порошків з алмазів низької міцності (АС6 і АС20), які використовуються в шліфувальних кругах для механічної обробки виробів. Раніше ми [17] показали, що термічна обробка може ефективно впливати на властивості зерен синтетичного алмазу з використанням феросплавів.
Зверніть увагу, що при нагріванні алмаз окислюється. Температура початку окислення оцінюється в 700–750 °С. А якщо нагріти до більш високих температур, то зустрінемося з явищем графітизації, а отже, з поступовим зникненням алмазу. Графітізація алмазу — вимушена перебудова кубічної решітки алмазу в гексагональну решітку графіту, що відбувається при досить високих температурах (1450–2000 °С), що відповідає умовам розриву зв’язків атомів у ґратці, їх перерозподілу та зміни відстані між кристалографічними площинами. Графітізація відбувається зі збільшенням об’єму в 1,5 рази, тому формування зародка відбувається шляхом подолання пружного опору середовища. У місці утворення графіту алмаз сильно напружений. Ідеальний кристал алмазу графітований переважно на поверхні. При наявності включень в алмазі графітизація може відбуватися і в об’ємі кристала [18].
Взагалі графітизація алмазу зумовлена його каталітичним фазовим перетворенням у графіт під дією кисню. Отже, температура початку графітизації в інтервалі температур до 1900 °С визначається наявністю кисню в зоні контакту з алмазом. У роботі [19] було висловлено припущення, що подібний вплив на графітизацію має надавати будь-яке середовище, що взаємодіє з алмазом, наприклад, хімічно активні карбідоутворюючі метали: Si, Ti, Cr, V, Mn, Fe, Co, Ni, і більшою мірою ті метали, у контакті з якими міжфазна енергія алмазу мінімальна. Графітізація алмазу при спіканні визначається спільною дією металу і кисню. У міру посилення каталітичного впливу на процес фазового перетворення алмазу в графіт під час спікання метали розташовуються наступним чином: Si, W, Ti, Ni, Cr, Mn. Енергія активації фазового перетворення алмазу в графіт максимальна для Si (168 кДж/моль) і мінімальна для Mn (55 кДж/моль). Вплив металів, які хімічно взаємодіють з алмазом, на процес його фазового перетворення в графіт зводиться в основному до різкого збільшення швидкості утворення поверхневого вуглецю за рахунок зменшення вільної поверхневої енергії алмазу на межі з металом і зменшення енергії активації процесу. Оцінка кінетики карбідоутворення в системі росту карбідного шару на поверхні алмазу в умовах, що відповідають його стабільності, показує, що при взаємодії алмазу з металами в цьому випадку його фазове перетворення в графіт не відбувається [19].
У даній роботі [20] представлено дослідження графітизації мікрокристалів синтетичного алмазу кубооктаедричної форми та морфологічної та структурної еволюції, що відбувається при 1600 °C під час вакуумного відпалу.
У зв’язку з вищесказаним звернемо увагу на роботу [21], дещо теоретичну, але присвячену високотемпературному впливу на алмаз і в якій запропоновано простий метод розрахунку верхньої межі температури плавлення алмазу, заснований на вивченні площинних дефектів у ньому.
3. РЕЗУЛЬТАТИ ТА ЇХ ОБГОВОРЕННЯ
Зауважимо також, що при нагріванні достатньо міцних (АС50–АС100) синтетичних алмазів важливим фактором, що викликає розтріскування зерен, є внутрішні температурні напруження, що виникають внаслідок термопружного неузгодженості включень твердого розчину металу-розчинника (Ni+Mn) і кристалічної решітки алмазу [22]. Включення металу-розчинника зберігаються в алмазі після синтезу і зосереджені переважно в площині (111). Через те, що модуль пружності цієї евтектики та її коефіцієнт теплового розширення суттєво (приблизно в 3,9 рази) відрізняються від відповідних властивостей алмазу, при нагріванні до досить високих температур, наприклад, 1400–1600 °C під час спікання з карбідною матрицею, включення розширюється, створюючи внутрішній тиск у порожнині, що призводить до руйнування зерна. руйнування, яке супроводжується виділенням на його поверхню крапель металу [23]. Моделювання та оптимізація параметрів продуктивності подрібнення наведено в роботах [24,25,26].
Все це, наведене вище, якраз і показує, що алмазні зерна досить високої міцності (AC50–AC200) більш вразливі до нагрівання, на відміну від алмазних зерен низької (AC4–AC6) міцності, і можуть бути зруйновані при досить високому (до 1000 °C) нагріванні. На алмазах низької міцності з розвиненою морфологією виділення металів-розчинників на поверхню при нагріванні не тільки не призводить до розтріскування зерен, але й призводить до заповнення дефектів поверхневих порожнин або пористого простору зерен. Тому необхідно враховувати такі дефекти, а саме розглядати це не як негативний, а як позитивний фактор при пошуку шляхів підвищення зносостійкості шліфувальних кругів за рахунок можливих змін домішкового складу поверхні зерен або заповнення порового простору зерен необхідними функціональними речовинами, спрямованого, наприклад термічного, впливу на стан поверхні алмазних зерен.
У літературі є деякі дані щодо руху домішок в алмазах [15, 16, 27] під час їх термічної обробки, але дослідження такого широкого спектру домішок, а отже, і значень питомої магнітної сприйнятливості алмазних зерен, не проводилися, тому в даній статті увагу було приділено цьому напряму. Слід зазначити, що звертаємо увагу на спрямований термічний вплив, оскільки цей напрямок має призводити до переміщення домішок в алмазі в напрямку поверхневих шарів, сприяти їх виходу в пори та тріщини і, як наслідок, підвищувати міцність зерна, а отже, і зносостійкість шліфувальних кругів.
На першому етапі, для отримання незалежної оцінки такого явища, як наявність високих домішок на поверхні алмазів, зразки синтетичних алмазів, виготовлених у системах росту Fe–Si–C і Ni–Mn–C двох фракцій для кожної системи (магнітної та немагнітної), які пройшли термообробку при 800 °С, були передані до Інституту проблем матеріалознавства імені Францевича НАН України. За допомогою скануючої електронної мікроскопії (РЕМ) оцінено вміст алмазів з різною магнітною сприйнятливістю домішок і включень та їх елементний склад. На приладі Cameca SX-50 проведено поелементний аналіз гладких і рельєфних поверхонь огранювання кристалів алмазу після термічних впливів. Елементний аналіз поверхонь граней кристалів синтетичного алмазу, виготовлених в обох системах Ni–Mn–C та Fe–Si–C після їх термічної обробки, показав, що на поверхнях граней алмазу є мішки та вкраплення, які під впливом високотемпературного нагріву через тріщини та пори вийшли на поверхню граней кристалів (рис. 1).
Встановлено, що ці утворення домішок і включень на поверхнях граней кристалів в основному складаються з елементів розчинного сплаву. Для синтетичних алмазів магнітної фракції, виготовлених у системі Ni–Mn–C, основний склад складають домішки Mn, Ni та O, а для немагнітних алмазів виявляються лише сліди O та Ni.
На поверхнях граней алмазів системи Fe–Si–C основний склад утворень складають такі елементи, як: Si, Al, Fe, O, Ca. У результаті дослідження зроблено висновок, що поверхні граней кристалів алмазу системи Fe–Si–C мають більш спрямований мікрорельєф порівняно з кристалами алмазу системи Ni–Mn–C. Таким чином, наведені досліди показали, що при термічному впливі на алмази відбуваються певні зміни вмісту елементів розчинного сплаву у включеннях і домішках магнітної фракції, про що можна судити по зміні їх магнітних властивостей.
Для цього на другому етапі досліджень для кожної з цих систем було відібрано по два зразки фракційного складу алмазів: магнітний (з найбільшим вмістом домішок) і слабомагнітний (з найменшим вмістом домішок), які піддавали термічній обробці від 500 до 1000 °С з витримкою 20 хв. Одночасно оцінювали втрату маси відповідного зразка порошку при нагріванні до тих же температур. Встановлено, що обидві досліджувані системи характеризуються наявністю температурного інтервалу, де зростає питома магнітна сприйнятливість алмазного порошку, але характер залежностей «температура – питома магнітна сприйнятливість» різний.
Магнітна сприйнятливість алмазних порошків Fe–Si–C зростає і досягає максимуму при температурі термообробки 800 ˚С. Цей ефект однаковий як для магнітних (рис. 2, а), так і для немагнітних порошків (рис. 2, б), але саме за наявності великої кількості включень, як і очікується з нашого припущення, ефект більш відчутний.
Зауважимо, що з підвищенням температури втрата маси алмазного порошку зростає, причому на менш магнітних порошках така втрата більш відчутна і при 1000 °C в обох випадках значно зростає, а отже значно знижує питому магнітну сприятливість, фактично повертаючись до вихідного стану.
Магнітна сприйнятливість синтетичних алмазних порошків призвела до того, що система Ni–Mn–C також змінюється зі зміною температури термообробки, але природа змін зовсім інша, ніж у алмазів Fe–Si–C. Також спостерігається ефект збільшення питомої магнітної сприйнятливості і також при термообробці температура 800 °C досягає максимуму.
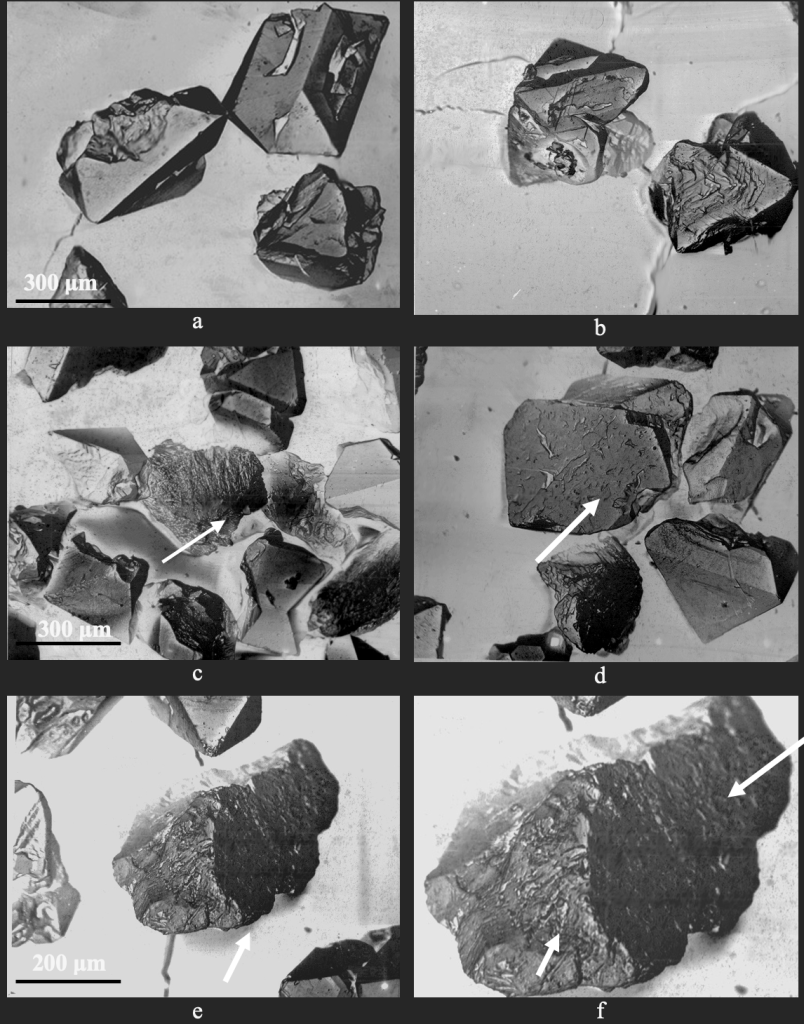
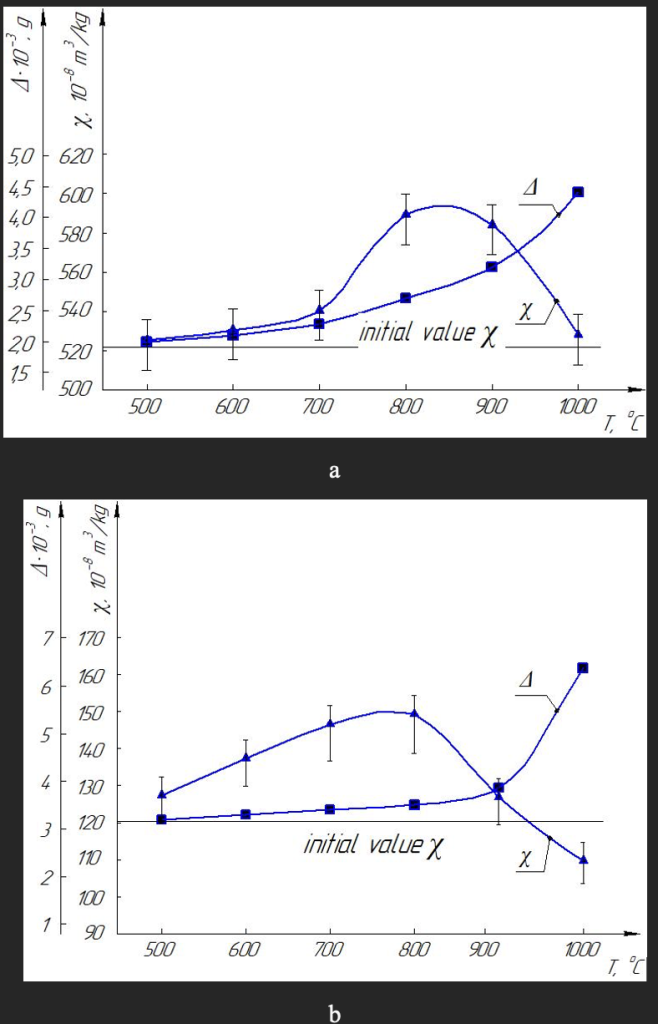
Але це відбувається тільки в магнітних порошках (рис. 3а), а для немагнітних порошків воно фактично відсутнє (рис. 3б). На нашу думку, це пов’язано з відносно низьким вмістом включень у таких алмазах, кількість яких недостатня для позитивного ефекту підвищення ефекту магнітної сприйнятливості. Серед іншого відзначимо, що з підвищенням температури, як і в алмазах системи Fe–Si–C, також зростає втрата маси алмазного порошку, але в алмазах системи Ni–Mn–C така втрата значно більша, і це, ймовірно, впливає на те, що при перевищенні температури 800 °C в обох випадках (див. рис. 3) значення питомої сприйнятливості значно знижується від значень для вихідного, не термічно обробленого порошку.
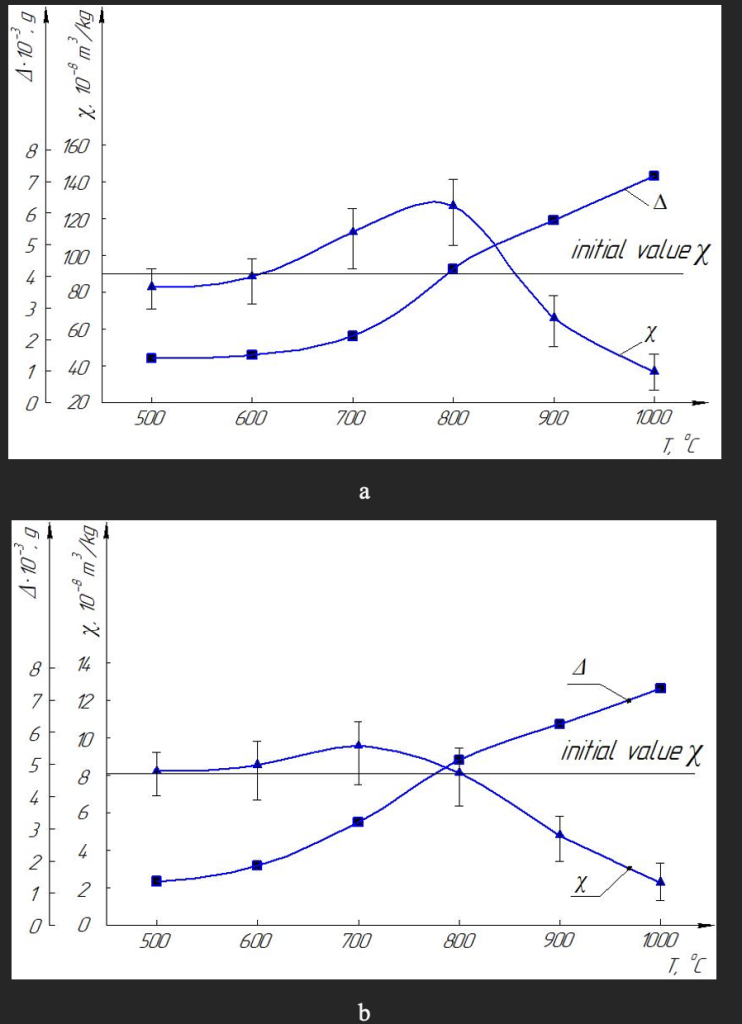
Наведені закономірності свідчать про те, що для магнітних зерен можна очікувати збільшення значень міцності (руйнівного навантаження) алмазних зерен під час термообробки. Міцність зерна алмазних шліфпорошків АС6 160/125 визначали за методикою ДСТУ 3292-95 після термообробки ряду магнітних і немагнітних фракцій системи Fe–Si–C, а також Ni–Mn–C.
Динаміка зміни міцності найбільш магнітних алмазних порошків обох систем синтезу в залежності від значення температури термообробки наведена на рис. 4. Встановлено, що міцність алмазів системи Fe–Si–C із підвищенням температури термообробки до 700 ºC залишається такою ж, як і вихідна, зростає при 800 і 900 ºC.
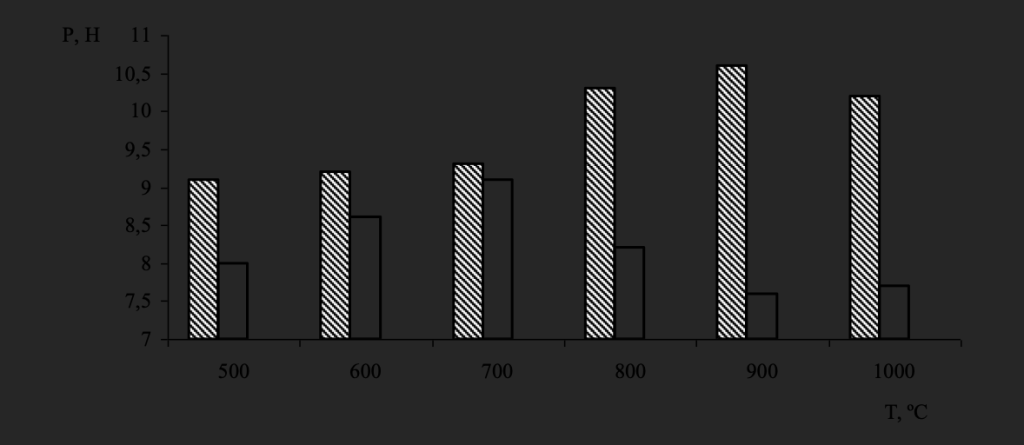
А потім має спадний характер, починаючи з 900 ºC. При цьому міцність виділеної магнітної фракції шліфувального порошку алмазів системи Ni–Mn–C зростає при 700 ºС, а потім зменшується.
Загальний характер зміни міцності зерна нагадує характер зміни величини магнітної сприйнятливості при термообробці. Тому ми проаналізували весь масив отриманих даних щодо значень міцності зерна та відповідних значень питомої магнітної сприйнятливості ряду магнітних і немагнітних зерен фракцій системи Fe–Si–C (рис. 5, а) та Ni–Mn–C (рис. 5, б). Аналіз даних рис. 5 видно, що як для зерен синтетичного алмазу системи Ni–Mn–C, так і для синтетичних алмазів системи Fe–Si–C ефект підвищення міцності зерен під дією термічної дії спрацьовує лише за наявності в алмазах достатньої кількості включень, а отже, і їх підвищеної магнітної сприйнятливості.
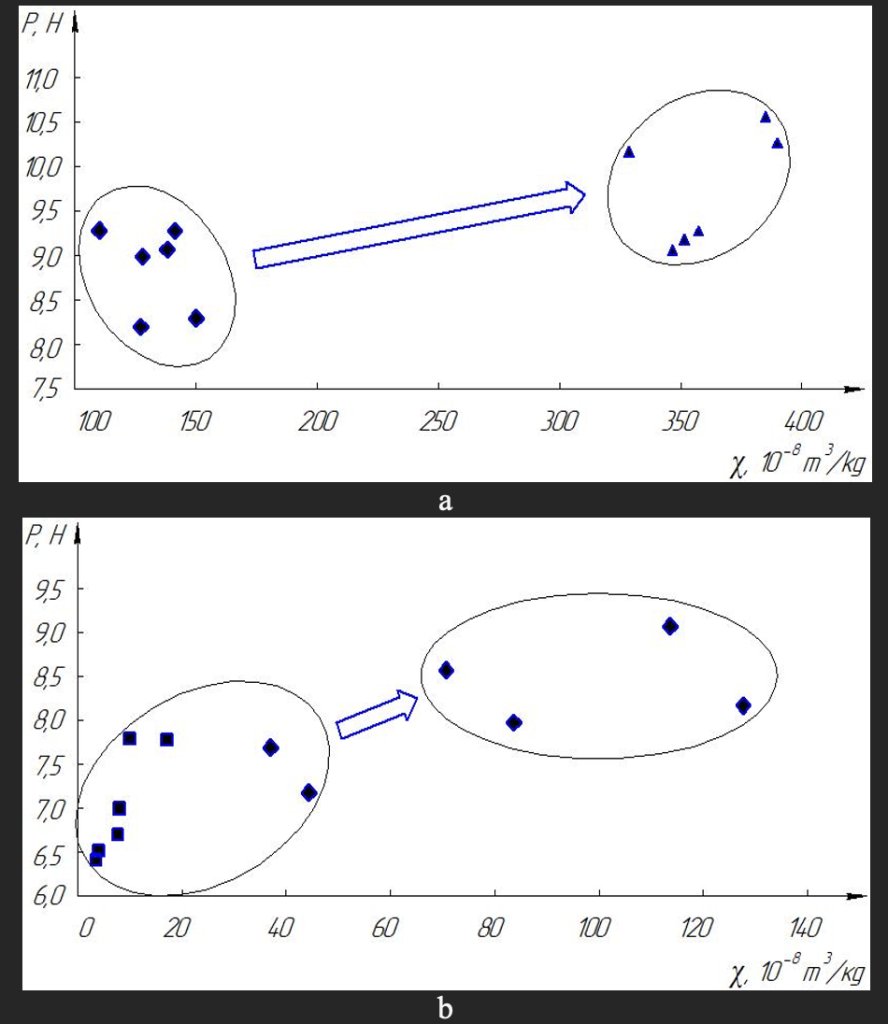
Fig. 5. Cluster correlation between specific magnetic susceptibility and destructive load (strength) of diamonds when heating magnetic and non-magnetic fractions of Fe–Si–C (a) and Ni–Mn–C (b).
Тому магнітні синтетичні алмази є системою Fe–Si–C і дають помітний ефект у підвищенні міцності зерен (див. рис. 4) під час термічної обробки, а отже, у можливості підвищення зносостійкості шліфувальних кругів. Це пов’язано насамперед з тим, що такі магнітні алмази, маючи значну (до 7 % мас.) кількість включень, мають значну масову базу для переміщення домішок і включень під час термообробки для забезпечення ефекту «заліковування» поверхневих дефектів алмазу.
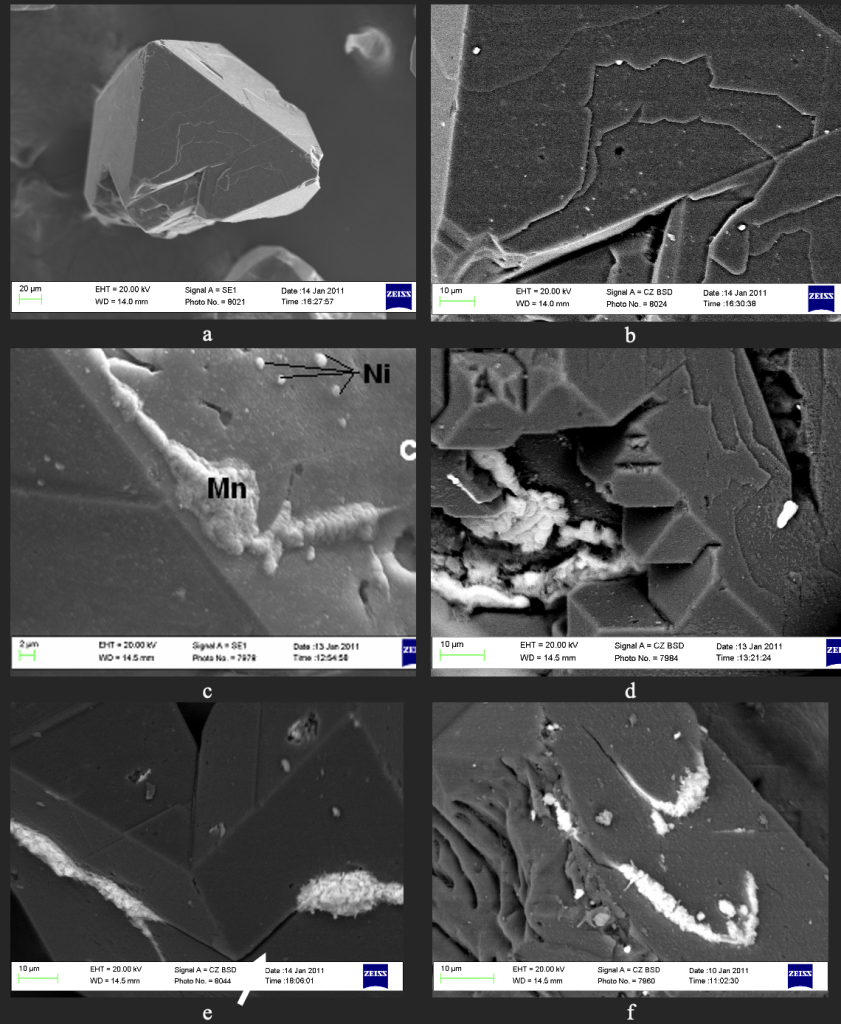
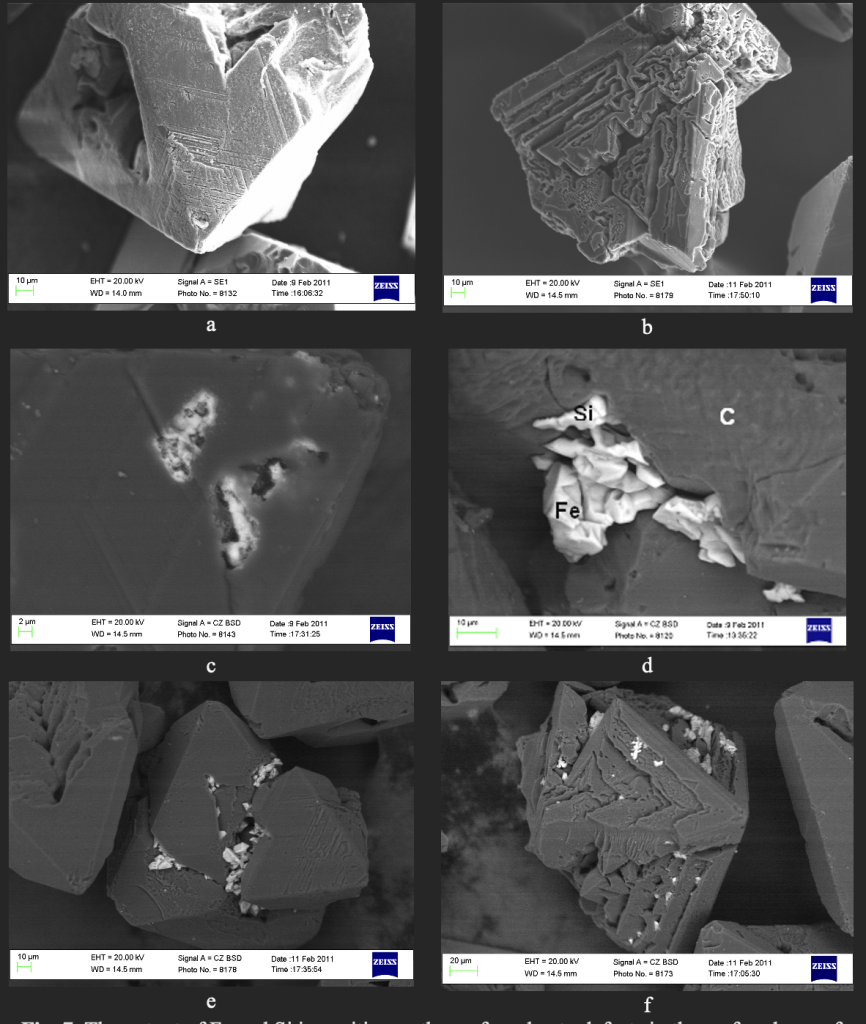
Щоб підтвердити це припущення, елементний склад і зміни поверхні алмазних зерен досліджували за допомогою електронного мікроскопа Zeiss EVO 50XVP. Для синтетичних магнітних зерен (c=90•10-8 м3/кг) характерна система Ni–Mn–C, наявність пор і тріщин (рис. 6а, б). Встановлено, що після термообробки при 700 °С (рис. 6в, г) та 1000 °С (рис. 6д, е) спостерігається вихід включень і заповнення тріщин і пор. Так само магнітна фракція синтетичного алмазу, виготовленого в системі вирощування Fe–Si–C (c=521•10-8 м3/кг), характеризується наявністю пор і тріщин (рис. 7а, б). Встановлено, що після термічної обробки при 800 °С (рис. 7в, г) та 1000 °С (рис. 7д, е) відбувається вихід включень і заповнення тріщин і пор.
Аналіз елементного складу включень і домішок у порах, тріщинах і на поверхні алмазних зерен проводили для синтетичних алмазів, виготовлених у системі вирощування Fe–Si–C (c=521•10-8 м3/кг) після термічної обробки при 800 °С (рис. 8, табл. 1). Аналіз даних Таблиця 1 свідчить про переважну присутність Fe та Si у цих домішках та включеннях.
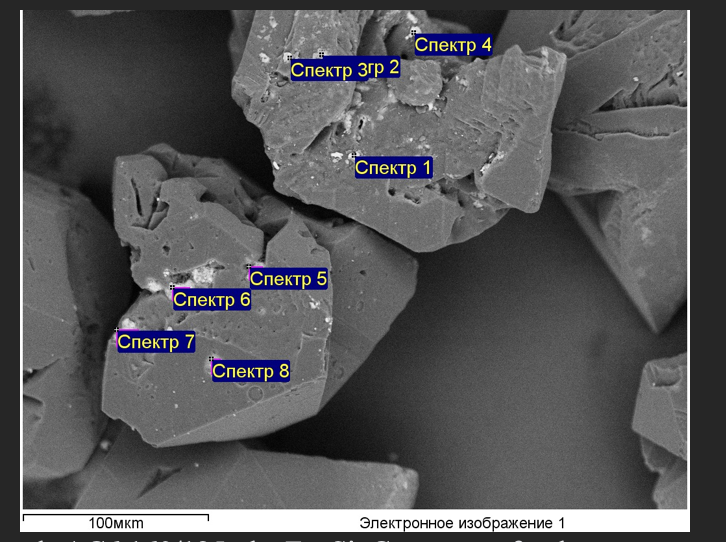
Table 1. Elemental composition of inclusions in the pores and on the surface of the grains (see Fig. 8).
Spectrum | Content of elements, % wt. | ||||||
C | O | Si | Fe | Cr | Mn | Ni | |
1 | 42,28 | 34,96 | 2,66 | 18,60 | 0,71 | 0,50 | 0,23 |
2 | 61,01 | 18,87 | 10,19 | 1,54 | 5,23 | 1,35 | 1,42 |
3 | 77,09 | 16,32 | 2,44 | 3,37 | 0,33 | 0,28 | 0,16 |
4 | 33,22 | 37,70 | 4,15 | 22,83 | 0,63 | 0,85 | 0,52 |
5 | 44,67 | 23,14 | 20,32 | 0,63 | 1,29 | 9,39 | 0,38 |
6 | 31,78 | 16,68 | 25,45 | 3,22 | 1,52 | 10,99 | 0,34 |
7 | 25,33 | 45,47 | 23,16 | 1,14 | 0,23 | 4,53 | 0,13 |
8 | 26,39 | 29,18 | 32,72 | 0,06 | 0,79 | 10,05 | 0,76 |
Таким чином, викладене свідчить про те, що термічний вплив на досліджувані алмази малої міцності залежно від кількості, виду домішок і включень дозволяє змінювати поверхневий елементний склад алмазів, величину питомої магнітної сприйнятливості шліфувальних порошків, міцність алмазу, підвищувати його вартість, а отже, розраховувати на підвищення зносостійкості шліфувального інструменту.
Для цього попередньо нами алмази марки АС6 зернистістю 160/125 обох вищевказаних систем росту розподілили за значенням їх початкової питомої магнітної сприйнятливості: c=90•10-8 м3/кг для синтетичних алмазів, виготовлених у системі Ni–Mn–С, і c=521•10-8 м3/кг для синтетичних алмазів, виготовлених у Fe–Si–С. система росту. Алмази піддавали термічній обробці протягом 20 хвилин при температурі 700 °C для першого та 800 °C для другого (див. рис. 4). Потім виготовляли шліфувальні круги з однаковими характеристиками, що містили алмази з різним вмістом включень і досліджували в однакових умовах.
Виділені в магнітному полі фракції порошку зернистістю 160/125 були випробувані при обробці твердого сплаву ВК8. Для дослідження було виготовлено чотири шліфувальні круги форми 12A2-45° AC6 160/125 50 M1-10 з використанням алмазів з різною питомою магнітною сприйнятливістю. Два колеса мали оригінальні алмази для обох систем вирощування, а інші два алмази були термічно оброблені, як описано вище. Обробка твердого сплаву ВK8 проводилася на верстаті 3Б642 торця колеса. Режими обробки: швидкість обертання колеса – 15 м/с, поздовжня подача – 0,6 м/хв, поперечна подача – 0,05 мм/пдв.год. Мастильно-охолоджуюча рідина – розчин соди. Зносостійкість шліфувальних кругів оцінювали за відносною вартістю алмазів qp (табл. 2).
Table 2. Relative costs of diamonds in wheels when grinding a hard alloy ВK8 (Q = 300 mm3/min)
Growth system | Condition of diamond grains | χ, х108 m3/kg | Нр, Н | Costs, qр, mg/g |
Ni–Mn–С | Initial | 90 | 7,8 | 3,7 |
Heat treated | 150 | 9,1 | 2,3 | |
Fe–Si–С | Initial | 521 | 8,8 | 1,9 |
Heat treated | 589 | 10,3 | 0,9 |
Аналіз даних показав, що в залежності від системи синтезу, домішок і включень в алмазах і, відповідно, величини їх питомої магнітної сприйнятливості термообробка зерен може збільшити до 2 разів зносостійкість алмазного шліфувального інструменту при шліфуванні твердого сплаву.
4. ВИСНОВОК
Важливою особливістю алмазних порошків, яка впливає на зносостійкість алмазних інструментів, є система росту, в якій вони синтезовані. Знаючи, в якій ростовій системі синтезовано алмаз, можна контролювати його фізико-механічні та фізико-хімічні характеристики.
Показано, що алмази містять включення елементів складу сплав-розчинник і їх можна розділити на магнітну та немагнітну (мінімальні значення магнітного значення) фракції. Це дозволяє контролювати властивості алмазів, наприклад, термообробку.
Досліджувані алмази малої міцності, що мають структурні дефекти і дефекти поверхні, можуть бути міцними сторонами кристала при певній температурі впливу на них.
Вплив термічної обробки на алмазні зерна з високими (магнітними) і малоцінними (немагнітними) включеннями елементів у складі сплав-розчинник різних систем росту Ni–Mn–C і Fe–Si–C показав, що це дозволяє контролювати міцність таких зерен, що позитивно впливає на їх застосування в інструменті.
СПИСОК ЛІТЕРАТУРИ
- Lavrinenko, V.I., Ilnitskaya, G.D., Petasyuk, G.A., at al. A study of the potential of improving performance of AS20 diamond powders through altering their dimensional and physico-chemical characteristics. Journal of Superhard Materials, 40 (4), 274–281. (2018).
- Borimsky, A.I., Delevi, V.G., Nagorny, P.A. Kinetics of diamond formation and growth in the Fe-Si-C system [in Russian]. Superhard Materials, 3, 9-14. (1999).
- Deng, A., Lu, J., Li, D.-X., Wang Y.-H. Exploring the activation energy of diamond reacting with metals and metal oxides by first-principle calculation. Diamond and Related Materials, 118, 108522. (2021).
- Piazzi, M., Morana, M., Coisson, M., Marone, F., Campione, M., Bindi, L., Jones, A.P., Ferrara, E., Alvaro, M. Multi-analytical characterization of Fe-rich magnetic inclusions in diamonds.Diamond and Related Materials, 98, 107489. (2019).
- Li, J.-W., Fang, W.-J., Wan, L., Liu, X.-P., Hu, W.-D., Cao, D., Han, K., Li, Y.-Y., Yan, Y.-G.: Research on the bonding properties of vitrified bonds with porous diamonds and the grinding performance of porous diamond abrasive tools. Diamond and Related Materials. 123, 108841. (2022).
- Yang, B., Lu, W.-Z., Feng, W., Yang, X., Zuo, D.-W. Adsorption and deposition of micro diamond particles in preparing diamond magnetic abrasives by electroless composite plating. Diamond and Related Materials, 73. 137-142. (2017).
- Kawasegi, N., Ozaki, K., Morita, N., Nishimura, K., Sasaoka, H. Single-crystal diamond tools formed using a focused ion beam: Tool life enhancement via heat treatment. Diamond and Related Materials, 49, 14-18. (2014).
- Geis, M.W., Hollis, M.A., Turner, G.W., Daulton, J., Varghese, J.O., Klyukin, K., Wang, J., Yildiz, B., Zhang, B. Controlling the carrier density of surface conductive diamond. Diamond and Related Materials, 122, 108775. (2022).
- Escobar, J.V., Chakravarty, A., Putterman, S.J.. Effect of anodic oxidation of single crystal boron doped diamond on tribocurrent and macroscopic friction force with metals. Diamond and Related Materials, 36, 8-15. (2013).
- Sha, X.-H., Yue, W., Zhang, H.-C., Qin, W.-B., She, D.-S., Wang, C.-B. Thermal stability of polycrystalline diamond compact sintered with boron-coated diamond particles. Diamond and Related Materials, 104, 107753. (2020).
- Wan, Q.-H., Zou, L., Liu, S.-Q., Wang, T.-T., Chen, S.-T., Huang, Y. Investigation on abrasive wear mechanism of single diamond grain in flexible scribing titanium alloy. Diamond and Related Materials, 120, 108631. (2021).
- Liang, Y.-F. Zheng, Y.-T., Wei, J.-J., Jia, X., Zhu, X.-H., An, K., Liu, J.-L., Chen, L.-X., Li, C.-M.. Effect of grain boundary on polycrystalline diamond polishing by high-speed dynamic friction. Diamond and Related Materials, 117, 108461. (2021).
- Chmir, M.Ya., Mogilnikov, V.A., Troitskiy, N.A., Gerasimenko, V.K. Interaction of synthetic diamonds with machined materials at diamond and diamond-electrochemical grinding [in Russian]. Electrochemical and Electrophysical Methods of Materials Processing: Collection of Scientific Works, Tula, 1991. pp. 52-59.
- Wu, X.-Z., Li, L.-Y., Zhang, W., Song, M.-X., Yang, W.-L., Peng, K. Effect of surface roughening on the interfacial thermal conductance of diamond/copper composites. Diamond and Related Materials, 98, 107467. (2019).
- Belyankina, A.V. Influence of high-temperature annealing on structure of single crystal of synthetic diamond [in Russian]. Synthetic Diamonds, 3, 22-24. (1971).
- Bacon, A. Investigation of changes occurring in diamond powders during reheating [in Russian]. Superhard Materials, 6, 20-23. (1983).
- Shulzhenko, A.A., Prikhna, T.O., Ilnytska, H.D., Lavrinenko, V.I., Borymskii, O.I., Sokolov, A.N., Tkach, V.N., Smokvyna, V.V., Zaitseva, I.N., Tymoshenko, V.V. Comparison of the dimensional, physical, mechanical and operational characteristics of as6 and AS20 synthetic diamond powders synthesized in the Ni‒Mn‒C and Fe‒Si‒C systems. Journal of Superhard Materials, 43 (1), 1–14. (2021).
- Tsypin, N.V. Wear resistance of composite diamond-containing materials for drilling tools [in Russian]. Nauk. dumka, Kyiv, 1983. – 192 pp.
- Nozhkina, A.V. Influence of metals on phase transformation of diamond into graphite [in Russian]. Superhard Materials, 3, 11-15. (1988).
- Bokhonov, B.B., Dudina, D.V., Sharafutdinov, M.R. Graphitization of synthetic diamond crystals: A morphological study. Diamond and Related Materials, 118, 108563. (2021).
- Kondrin, M.V., Lebed, Y.B., Brazhkin, V.V. Intrinsic planar defects in diamond and the upper limit on its melting temperature. Diamond and Related Materials, 110, 108114. (2020).
- Lavrinenko, V.I., Ilnitskaya, G.D., Sheiko, M.N., Dobroskok, V.L., Ostroverkh, Ye.V., Solod, V.Yu. Improving the performance characteristics of synthetic diamond for high-precision diamond dressing tool. Science and Innovation, 17 (6), 72–82. (2021).
- Novikov, N.V., Maistrenko, A.L., Kulakovsky, V.N. Fracture resistance of superhard composite materials [in Russian]. Nauk. dumka, Kyiv, 1993. – 220 pp.
- Tonkonogyi, V., Dašić, P., Rybak, O., Lysenko, T. Application of the modified genetic algorithm for optimization of plasma coatings grinding process. Lecture Notes in Networks and Systems (LNNS), 76, 199–211. (2020). doi: 10.1007/978-3-030-18072-0_23.
- Tonkonogyi, V., Yakimov, A., Bovnegra, L. Increase of performance of grinding by plate circles. Lecture Notes in Networks and Systems (LNNS), 42, 121–127. (2019). doi: 10.1007/978-3-319-90893-9_14.
- Usov, A., Tonkonogyi, V., Dašić, P., Rybak, O. Modelling of temperature field and stress-strain state of the workpiece with plasma coatings during surface grinding. Machines, 7 (1), Article no. 20. (2019). doi: 10.3390/machines7010020.
- Belyankina, A.V., Multakh, L.M., Simkin, E.S., Sozin, Y.I., Tsypin, N.V. Investigation of changes occurring in diamonds during heating [in Russian]. Synthetic Diamonds, 1, 20-22. (1972).